Shearing forming method for annular outer rib cylindrical part
A technology of cylindrical parts and rings, which is applied in the field of shear forming of ring-shaped outer-reinforced cylindrical parts, can solve problems such as the difficulty in forming ring-shaped outer-reinforced structural parts, improve forming accuracy and structural reliability, and reduce equipment requirements and reduce The effect of energy consumption
- Summary
- Abstract
- Description
- Claims
- Application Information
AI Technical Summary
Problems solved by technology
Method used
Image
Examples
Embodiment
[0033] Example A method of shearing and forming a ring-shaped outer rib cylindrical part
[0034] Based on the cylindrical piece spinning forming process, the present embodiment selects the shearing wheel 4 and changes the working angle of the shearing wheel 4, so that the shearing surface of the shearing wheel 4 and the blank 1 of the cylindrical piece are formed The assembly surface is contacted, and then the adjustment of the working mode of the rotary wheel is realized: from the single spinning working mode to the shearing-spinning combined working mode; at the same time, the annular back pressure mold 2 is used to The barrel blank 1 imposes radial constraints. The method specifically includes the following steps:
[0035] S1. Making the tube blank: Machining the original tube-shaped piece to be processed, and then processing the end with a pressure shoulder after opening a hole in the circumferential direction to prepare a tube-shaped piece blank 1 with a pressure should...
PUM
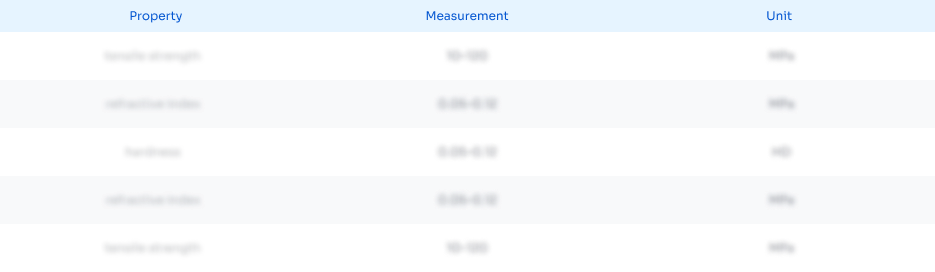
Abstract
Description
Claims
Application Information

- Generate Ideas
- Intellectual Property
- Life Sciences
- Materials
- Tech Scout
- Unparalleled Data Quality
- Higher Quality Content
- 60% Fewer Hallucinations
Browse by: Latest US Patents, China's latest patents, Technical Efficacy Thesaurus, Application Domain, Technology Topic, Popular Technical Reports.
© 2025 PatSnap. All rights reserved.Legal|Privacy policy|Modern Slavery Act Transparency Statement|Sitemap|About US| Contact US: help@patsnap.com