Method, device and equipment for distributing propulsive force of synchronous pushing and splicing system of shield tunneling machine and medium
A distribution method and propulsion technology, which are applied in the field of shield tunnel construction technology and equipment, can solve the problems of inability to realize the distribution of the propulsion force of the remaining oil cylinders, and achieve the reduction of power loss, shield attitude and propulsion speed assurance, and accurate adjustment. Effect
- Summary
- Abstract
- Description
- Claims
- Application Information
AI Technical Summary
Problems solved by technology
Method used
Image
Examples
Embodiment Construction
[0106] The following will clearly and completely describe the technical solutions in the embodiments herein in conjunction with the accompanying drawings in the embodiments herein. Obviously, the described embodiments are only some of the embodiments herein, not all of them. Based on the embodiments herein, all other embodiments obtained by persons of ordinary skill in the art without making creative efforts fall within the scope of protection herein.
[0107] It should be noted that the terms "first" and "second" in the description and claims herein and the above drawings are used to distinguish similar objects, but not necessarily used to describe a specific order or sequence. It is to be understood that the data so used are interchangeable under appropriate circumstances such that the embodiments herein described herein can be practiced in sequences other than those illustrated or described herein. Furthermore, the terms "comprising" and "having", as well as any variations ...
PUM
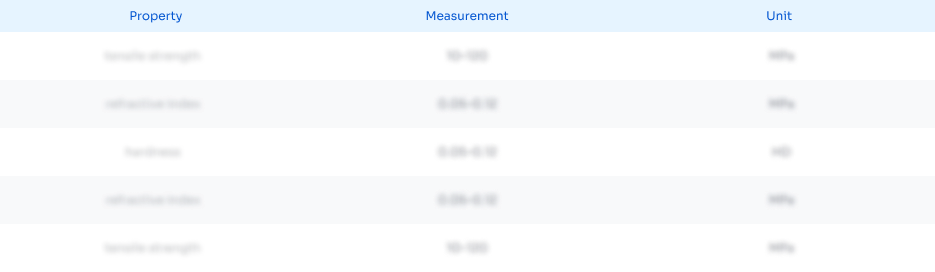
Abstract
Description
Claims
Application Information

- Generate Ideas
- Intellectual Property
- Life Sciences
- Materials
- Tech Scout
- Unparalleled Data Quality
- Higher Quality Content
- 60% Fewer Hallucinations
Browse by: Latest US Patents, China's latest patents, Technical Efficacy Thesaurus, Application Domain, Technology Topic, Popular Technical Reports.
© 2025 PatSnap. All rights reserved.Legal|Privacy policy|Modern Slavery Act Transparency Statement|Sitemap|About US| Contact US: help@patsnap.com