Adjustable gravity loading garment for simulating spine physiological load
A gravity-loaded and adjustable technology, applied in the field of space suit design, can solve problems such as human injury, achieve the effects of preventing discomfort, good wear and tear performance, and avoiding non-specific low back pain
- Summary
- Abstract
- Description
- Claims
- Application Information
AI Technical Summary
Problems solved by technology
Method used
Image
Examples
Embodiment 1
[0067] Such as Figure 6a , 6b , 6c shows the front, back and side views of the garment of Example 1, using polyester-cotton blended yarn to weave double rib weave to form a non-elastic fabric 7 to form the first gripping area 1 of the garment. Nylon ammonia core-spun yarn is used to weave the composite weft-knitted fabric. The transverse density of the fabric increases gradually from top to bottom, and the vertical density of the fabric increases with the increase of the circumference of the human body, forming a gradient elastic fabric 8. The control strips 9 are spaced at intervals of 10cm. The warp weaving is woven into the composite weft knitting to jointly form the variable elastic fabric 10 to form the initial gravity loading area 2 of the garment. The first holding area 1 and the initial gravity loading area 2 are woven by integral molding on a knitting machine. The hook-like fabric 11 is selected as the connection device I, and the fluffy fabric 12 is used as the co...
Embodiment 2
[0070] Such as Figure 7a , 7b , 7c shows the front, back and side views of the garment of Example 2, using polyester-cotton blended yarn to weave double rib weave to form a non-elastic fabric 7 to form the first gripping area 1 of the garment. Nylon ammonia core-spun yarn is used to weave the composite weft-knitted fabric. The transverse density of the fabric increases gradually from top to bottom, and the vertical density of the fabric increases with the increase of the circumference of the human body, forming a gradient elastic fabric 8. The control strips 9 are spaced at intervals of 10cm. The warp weaving is woven into the composite weft knitting to jointly form the variable elastic fabric 10 to form the initial gravity loading area 2 of the garment. The first holding area 1 and the initial gravity loading area 2 are woven by integral molding on a knitting machine. The metal wire 13 is selected as the connection device I, and the metal hook 14 is used as the connection ...
Embodiment 3
[0073] Such as Figure 8a , 8b , 8c shows the front, back and side views of the garment of Embodiment 3. This example shows the simplified structure of the knitted-based gravity-loaded garment after it has been stretched. It is divided into the first grip area 1, The gravity loading area 15 and the second gripping area 4 use the same fabric structure as above, that is, the non-elastic fabric 7 , the gradient elastic fabric 8 , the control strip 9 and the shape memory fabric 5 . Preferably, the shape memory fabric 5 can be sewn on both sides of the garment to better control the gradient elastic fabric 8 and help control the strip 9 to maintain the stability of the garment.
PUM
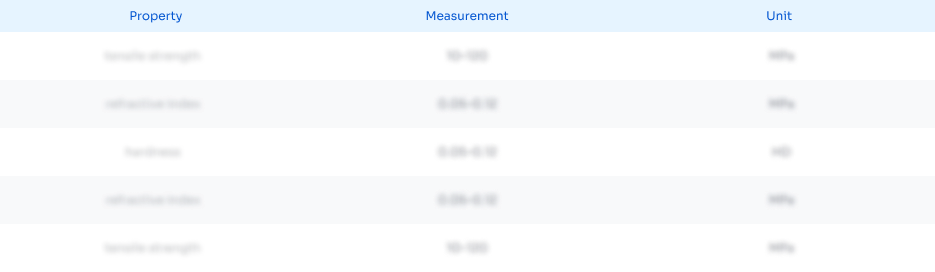
Abstract
Description
Claims
Application Information

- R&D
- Intellectual Property
- Life Sciences
- Materials
- Tech Scout
- Unparalleled Data Quality
- Higher Quality Content
- 60% Fewer Hallucinations
Browse by: Latest US Patents, China's latest patents, Technical Efficacy Thesaurus, Application Domain, Technology Topic, Popular Technical Reports.
© 2025 PatSnap. All rights reserved.Legal|Privacy policy|Modern Slavery Act Transparency Statement|Sitemap|About US| Contact US: help@patsnap.com