Manufacturing method of paper pulp molded product and paper pulp molding equipment for transferring wet blank by turner
A technology of pulp molding and manufacturing methods, which is applied in the direction of textiles and papermaking, conveyor objects, transportation and packaging, etc., which can solve the problems of difficult product surface calendering, long time-consuming, large heat loss, etc., to reduce creasing The effect of machine rate, production cost reduction, and easy hot-press demoulding
- Summary
- Abstract
- Description
- Claims
- Application Information
AI Technical Summary
Problems solved by technology
Method used
Image
Examples
Embodiment 1
[0066] Such as figure 1 As shown, in this embodiment, the pulp molding equipment for transferring the wet billet by the tumbler includes a machine frame, a suction filter forming device, a hot press setting device, a first wet billet transfer device, a second wet billet transfer device, a control system, and the like. In the middle of the lower frame 1a, a suction filter forming device 2 is arranged, above the suction filter forming device 2, a first wet base transfer device 7 is arranged, and a hot press setting device 3 is respectively provided on the left and right sides of the frame, respectively. It is a left heat press setting device 3L and a right heat press setting device 3R.
[0067] Such as figure 1 As shown, the frame 1 is composed of a lower frame 1a, an upper frame 1b, and a tie rod 1c, and the tie rod 1c fixes the lower frame 1a and the upper frame 1b together.
[0068] Suction filter forming device 2 contains suction filter forming mold 2a, suction filter form...
Embodiment 2
[0103] This embodiment is a simplification of Embodiment 1, such as Figure 6 As shown, the pulp molding equipment of the present embodiment that transfers the wet billet with the tumbler only contains one thermocompression setting device. In this embodiment, the pulp molding equipment for transferring the wet billet by the tumbler includes a frame 1, a suction filter molding device 2, a hot press setting device 3, a second wet billet transfer device 5, a first wet billet transfer device 7, a control system etc.
[0104] Because there is only one heat-press setting device, there is no distinction between the left heat-press setting device and the right heat-press setting device. The implementation principle is the same as that of Embodiment 1.
Embodiment 3
[0106] Such as Figure 7 , Figure 8 As shown, the pulp molding equipment for transferring wet billets by a tumbler includes a machine frame, a suction filter forming device, a hot press setting device, a first wet billet transfer device, a second wet billet transfer device, a control system, and the like.
[0107] Such as Figure 7 , Figure 8 As shown, on the left side of the pulp molding equipment where the tumbler transfers the wet billet, there is a receiving table 10 for placing the dried and shaped product 11 .
[0108] On the lower side of the upper frame from the left end to the right end, fix 2 (or 2 groups) left and right translation rails 8, and the left and right translation rails 8 span the top of the material receiving table 10, the top of the hot pressing lower die, and the top of the first wet billet transfer device 7 .
[0109] The suction filtration molding device and the first wet billet transfer device are the same as those in Embodiment 1 and Embodime...
PUM
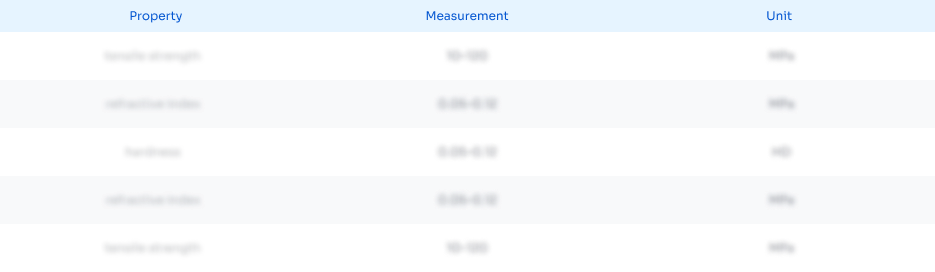
Abstract
Description
Claims
Application Information

- R&D
- Intellectual Property
- Life Sciences
- Materials
- Tech Scout
- Unparalleled Data Quality
- Higher Quality Content
- 60% Fewer Hallucinations
Browse by: Latest US Patents, China's latest patents, Technical Efficacy Thesaurus, Application Domain, Technology Topic, Popular Technical Reports.
© 2025 PatSnap. All rights reserved.Legal|Privacy policy|Modern Slavery Act Transparency Statement|Sitemap|About US| Contact US: help@patsnap.com