High-rigidity numerical control machine tool cross beam assembly
A technology of CNC machine tools and assembly parts, which is applied in the field of CNC machine tools, can solve the problems of linear guide rail stiffness reduction, linear guide rail uneven force, and shortened service life, so as to increase machining accuracy, maintain force uniformity, and improve use. The effect of longevity
- Summary
- Abstract
- Description
- Claims
- Application Information
AI Technical Summary
Problems solved by technology
Method used
Image
Examples
Embodiment Construction
[0028] In order to more clearly understand the above objects, features and advantages of the present invention, the present invention will be further described below in conjunction with the accompanying drawings and embodiments. It should be noted that, in the case of no conflict, the embodiments of the present application and the features in the embodiments can be combined with each other.
[0029] The present invention will be further described below in conjunction with the accompanying drawings and specific embodiments.
[0030] According to an embodiment of the present invention, such as Figure 1-9 displayed in:
[0031] The present invention provides a numerically controlled machine tool crossbeam assembly with strong rigidity, which includes a symmetrically arranged column body 1, and a crossbeam 2 is arranged across the top of the corresponding side of the column body 1, and the crossbeam 2 is an inverted U-shaped structure. One end of the back side of the beam 2 is ...
PUM
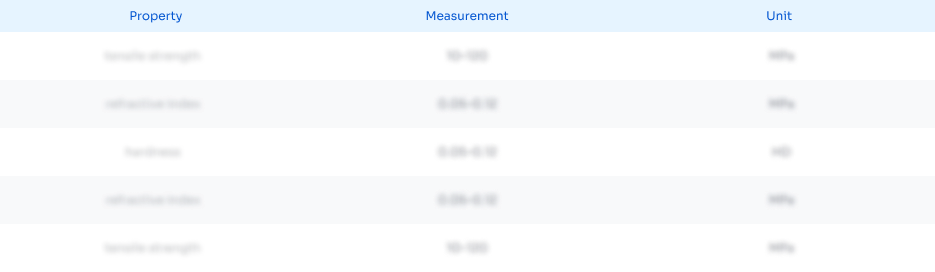
Abstract
Description
Claims
Application Information

- Generate Ideas
- Intellectual Property
- Life Sciences
- Materials
- Tech Scout
- Unparalleled Data Quality
- Higher Quality Content
- 60% Fewer Hallucinations
Browse by: Latest US Patents, China's latest patents, Technical Efficacy Thesaurus, Application Domain, Technology Topic, Popular Technical Reports.
© 2025 PatSnap. All rights reserved.Legal|Privacy policy|Modern Slavery Act Transparency Statement|Sitemap|About US| Contact US: help@patsnap.com