Torque vector distribution system, vehicle and torque vector distribution method
A distribution system and torque vectoring technology, applied in vehicle components, non-deflectable wheel steering, steering mechanism, etc., can solve the problems of heavy and complex torque vector distribution differential, energy consumption, high cost, etc., to facilitate unmanned driving. Controls, tight structures, space-saving effects
- Summary
- Abstract
- Description
- Claims
- Application Information
AI Technical Summary
Problems solved by technology
Method used
Image
Examples
Embodiment 1
[0041] Embodiment 1: A torque vectoring distribution system, which is provided with a driving part, on both sides of the driving part, a first bead tooth engagement device 4 and a second bead tooth engagement device 32 are connected through power transmission, on the first bead tooth engagement device 4 The first bead meshing wheel 3 is provided, and the first bead meshing wheel 3 is connected with the first torque output shaft 27 in a power transmission that can slide along the torque output shaft. The first toggling part 22 is connected, and the first toggling part 22 drives the first bead gear 3 to engage and separate the bead rings 29 of different diameters on the first bead gear 4 for power transmission. The second bead gear 32 is provided with a second bead gear 9, and the second bead gear 9 is connected to the second torque output shaft 13 in a power transmission that can slide along the torque output shaft. The second bead gear 9 It is connected with the second toggle ...
Embodiment 2
[0042] Embodiment 2: A kind of torque vector distribution system is provided with a driving part, and the driving part is composed of a driving gear 31, a deceleration part 7 for power transmission with the driving gear 31, and a power input part 6 for power transmission with the deceleration part 7, The power input part 6 is connected with the fuel-burning engine. Both sides of the driving gear 31 are connected with the first bead gear 4 and the second bead gear 32 through power transmission, the first bead gear 4 is provided with the first bead meshing wheel 3, and the first bead gear The wheel 3 and the first torque output shaft 27 are connected in a power transmission that can slide along the torque output shaft, and the first pinion meshing wheel 3 is connected with the first toggle part 22 that can slide along the torque output shaft, and the first toggle Part 22 drives the first bead gear 3 and the bead ring 29 of different diameters on the first bead gear 4 to engage a...
Embodiment 3
[0043] Embodiment 3: A torque vectoring distribution system is provided with a driving part, and the driving part is composed of a driving gear 31, a deceleration part 7 for power transmission with the driving gear 31, and a power input part 6 for power transmission with the deceleration part 7. Speed reduction part 7 is made up of reduction box 37, is located in reduction box 37 and the drive bevel gear 39 that carries out power connection with power input part 6, and the transmission bevel gear 35 that meshes with drive bevel gear 39 and drive gear 31 carries out power transmission is formed, power The input part 6 is connected with the new energy motor. Both sides of the driving part are connected with the first bead gear 4 and the second bead gear 32 through power transmission. The first bead gear 4 is provided with the first bead gear 3, and 3 is connected with the first torque output shaft 27 for power transmission that can slide along the torque output shaft, and the ...
PUM
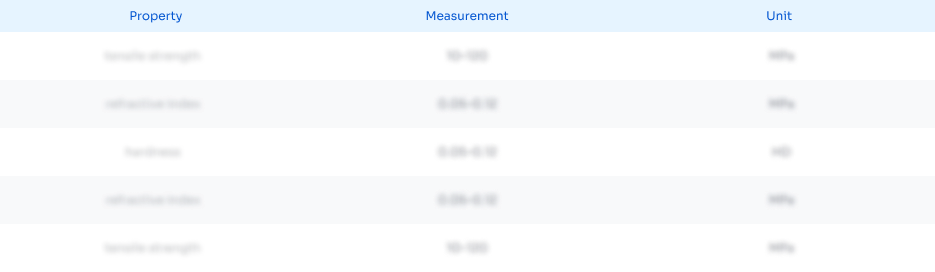
Abstract
Description
Claims
Application Information

- R&D Engineer
- R&D Manager
- IP Professional
- Industry Leading Data Capabilities
- Powerful AI technology
- Patent DNA Extraction
Browse by: Latest US Patents, China's latest patents, Technical Efficacy Thesaurus, Application Domain, Technology Topic, Popular Technical Reports.
© 2024 PatSnap. All rights reserved.Legal|Privacy policy|Modern Slavery Act Transparency Statement|Sitemap|About US| Contact US: help@patsnap.com