Forming method of large-size integrated body side outer panel
A technology of a side wall outer plate and a forming method, which is applied to the processing field of the steam side wall outer plate, can solve the problems of excessively large roll width and size of the blank, and reduce the procurement cost, the tooling projection cost and the difficulty in purchasing steel plates. improved effect
- Summary
- Abstract
- Description
- Claims
- Application Information
AI Technical Summary
Problems solved by technology
Method used
Image
Examples
Embodiment Construction
[0032] The principles and features of the present invention are described below in conjunction with the accompanying drawings, and the examples given are only used to explain the present invention, and are not intended to limit the scope of the present invention.
[0033] This embodiment discloses a forming method for a large-sized integrated side wall outer panel. By adopting this forming method, it is possible to solve the difficulty in purchasing raw materials due to the large width of the blank material plate that exists in the stamping production of the traditional super-large-sized side wall outer panel. Problems and the mold cannot be installed and the mold is difficult to lift and transfer due to the excessive size of the mold.
[0034] At the same time, in the present invention, since the side wall outer plate adopts the integral stamping and forming scheme, it also solves the problem of the large number of parts in the split side wall outer plate solution, which leads...
PUM
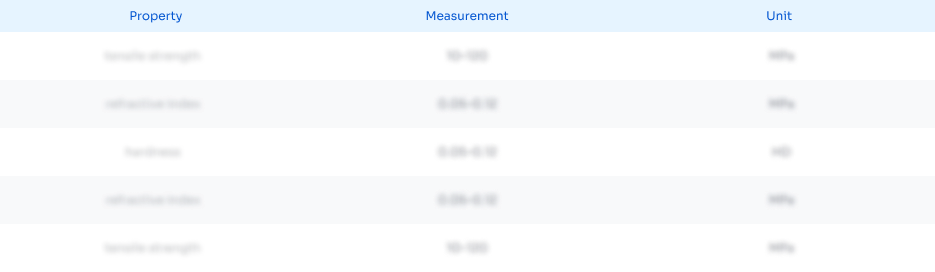
Abstract
Description
Claims
Application Information

- Generate Ideas
- Intellectual Property
- Life Sciences
- Materials
- Tech Scout
- Unparalleled Data Quality
- Higher Quality Content
- 60% Fewer Hallucinations
Browse by: Latest US Patents, China's latest patents, Technical Efficacy Thesaurus, Application Domain, Technology Topic, Popular Technical Reports.
© 2025 PatSnap. All rights reserved.Legal|Privacy policy|Modern Slavery Act Transparency Statement|Sitemap|About US| Contact US: help@patsnap.com