Magnetic-liquid composite planar multi-degree-of-freedom tuned mass damper
A technology for tuning mass damping and degrees of freedom, used in shock absorbers, shock absorbers, magnetic springs, etc. problem, to achieve the effect of convenient adjustment of damping size and resonance frequency, light weight and simple structure
- Summary
- Abstract
- Description
- Claims
- Application Information
AI Technical Summary
Problems solved by technology
Method used
Image
Examples
Embodiment Construction
[0031] In order to make the object, technical solution and advantages of the present invention clearer, the present invention will be further described in detail below in conjunction with the accompanying drawings and embodiments. It should be understood that the specific embodiments described here are only used to explain the present invention, not to limit the present invention.
[0032]The tuned mass damper of the present invention mainly consists of a magnet mover, a non-magnetic metal plate, shrapnel, damping fluid, a frame, a damping adjustment component and a stiffness adjustment component. A sealed chamber is formed between the rectangular ring frame and the non-magnetic metal plates parallel to each other through a pre-compressed elastic gasket with variable thickness. A magnet mover is arranged in the sealed chamber, and the magnet mover is distributed around the magnet mover. The shrapnel is connected with the ring frame to form a resonant unit. The permanent magne...
PUM
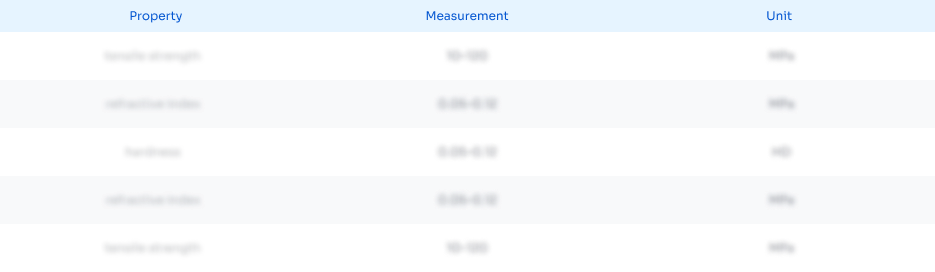
Abstract
Description
Claims
Application Information

- R&D Engineer
- R&D Manager
- IP Professional
- Industry Leading Data Capabilities
- Powerful AI technology
- Patent DNA Extraction
Browse by: Latest US Patents, China's latest patents, Technical Efficacy Thesaurus, Application Domain, Technology Topic, Popular Technical Reports.
© 2024 PatSnap. All rights reserved.Legal|Privacy policy|Modern Slavery Act Transparency Statement|Sitemap|About US| Contact US: help@patsnap.com