Welding module of semi-automatic hot plate welding equipment for plastic impeller
A hot plate welding and semi-automatic technology, which is applied to household components, household appliances, and other household appliances. It can solve problems such as weak welding, low production efficiency, and performance impact. It is easy to control the time and accuracy, and improve production efficiency. , Improve the effect of welding quality
- Summary
- Abstract
- Description
- Claims
- Application Information
AI Technical Summary
Problems solved by technology
Method used
Image
Examples
Embodiment Construction
[0017] The present invention will be further described below in conjunction with accompanying drawing.
[0018] like figure 1 As shown, a welding module of a semi-automatic hot plate welding equipment for plastic impellers includes a first backrest clamp assembly 6 for sleeve-mounting the front opening 4 of the impeller upper cover, and is used to fix the impeller upper cover 1 to the first backrest clamp assembly The first adjustment and deformation mechanism 7 on the 6, the second backrest clamp assembly 8 for sleeve installation of the impeller lower cover hub 5 and the second adjustment deformation mechanism for fixing the impeller lower cover 2 to the second backrest clamp assembly 8 9. The first backrest clamp assembly 6 is set opposite to the second backrest clamp assembly 8, and the contact points of the first adjustment deformation mechanism 7 and the second adjustment deformation mechanism 9 are provided with mutually engaging fan-shaped grooves 10 and fan-shaped pro...
PUM
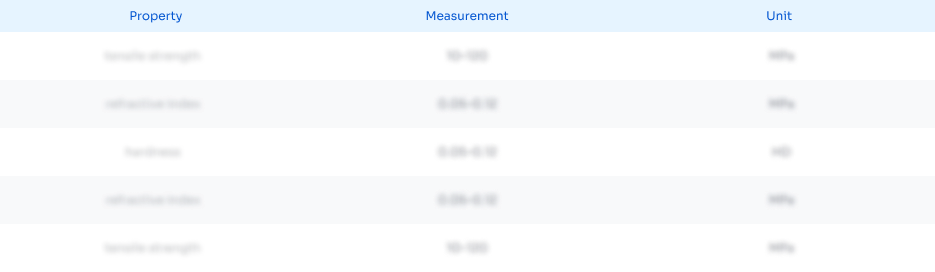
Abstract
Description
Claims
Application Information

- R&D Engineer
- R&D Manager
- IP Professional
- Industry Leading Data Capabilities
- Powerful AI technology
- Patent DNA Extraction
Browse by: Latest US Patents, China's latest patents, Technical Efficacy Thesaurus, Application Domain, Technology Topic, Popular Technical Reports.
© 2024 PatSnap. All rights reserved.Legal|Privacy policy|Modern Slavery Act Transparency Statement|Sitemap|About US| Contact US: help@patsnap.com