Textile operation equipment with thread layer carding structure
A technology for operating equipment and textiles, used in textiles and papermaking, spray/jet textile material treatment, fabric surface trimming, etc.
- Summary
- Abstract
- Description
- Claims
- Application Information
AI Technical Summary
Problems solved by technology
Method used
Image
Examples
Embodiment 1
[0043] Such as figure 2 , image 3 with Figure 4 As shown, a textile operation equipment with a line layer carding structure includes a base plate 1, a front plate 2, a rear plate 3, a U-shaped insert plate 4, a traction roller 5 and a fixed plate 6, and the front and back sides of the base plate 1 are respectively equipped with Front panel 2 and rear panel 3;
[0044] Specifically, the bottom plate 1 provides a relatively stable installation position for the components on the top, and is convenient to integrate the various components on the top, so that it is combined into a complete line layer carding structure. The bottom plate 1, the front plate 2 and the rear plate 3 three The latter is the outer frame of the textile handling equipment.
[0045] Two sets of U-shaped insert plates 4 arranged side by side are installed on the top of the bottom plate 1, and two sets of traction rollers 5 arranged side by side are installed on the front of the rear plate 3, and the front...
Embodiment 2
[0050] Such as figure 1 , Figure 5 with Image 6 As shown, the front of the front plate 2 is installed with the first roller 13 and the second roller 14, and the second roller 14 is located obliquely above the first roller 13, and the backs of the first roller 13 and the second roller 14 run through the back plate 3, the outer surfaces of the first roller 13 and the second roller 14 are equipped with threaded sleeves 15, and the outer surfaces of the two sets of threaded sleeves 15 are fitted with connecting cylinders 16 through thread fitting, and the outer surfaces of the connecting cylinders 16 are uniformly installed with The brush rod 17, the tail end of the brush rod 17 is equipped with multiple groups of evenly arranged arc-shaped protrusions 18.
[0051] Concretely, the first rotating roller 13 and the second rotating roller 14 can rotate under the drive of the motor, and then drive the threaded sleeve 15 installed on its outer surface, the connecting cylinder 16 an...
Embodiment 3
[0053] Such as figure 1 , Figure 7 with Figure 8 As shown, the bottom wall of the U-shaped board 4 is provided with a partition plate 19, and the top of the partition board 19 extends out of the inside of the U-shaped board 4, and the outer wall of one side of the partition board 19 is provided with a through groove 20. One side outer wall of the partition 19 is provided with two sets of moving slots 21 arranged up and down, and the two sets of moving slots 21 are respectively located above and below the through slot 20 .
[0054] The inner wall of the through groove 20 is equipped with two sets of moving blocks 22 arranged front and back, and the outer walls of both sides of the moving block 22 are equipped with rectangular blocks 23, and one of the outer walls of one set of long blocks 23 is installed with two sets of locking blocks arranged up and down. Nails 24, and one end of two groups of locking nails 24 penetrates the interior of two groups of moving grooves 21 and...
PUM
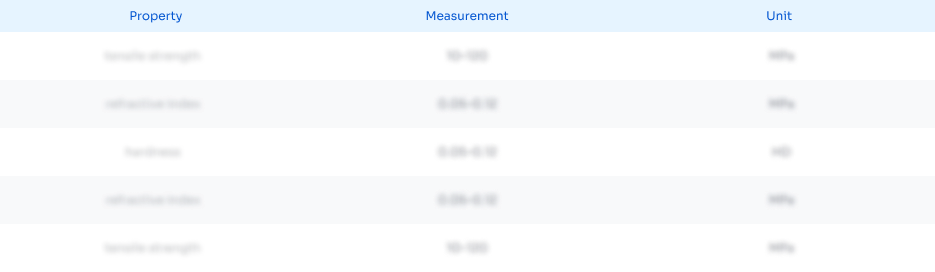
Abstract
Description
Claims
Application Information

- R&D
- Intellectual Property
- Life Sciences
- Materials
- Tech Scout
- Unparalleled Data Quality
- Higher Quality Content
- 60% Fewer Hallucinations
Browse by: Latest US Patents, China's latest patents, Technical Efficacy Thesaurus, Application Domain, Technology Topic, Popular Technical Reports.
© 2025 PatSnap. All rights reserved.Legal|Privacy policy|Modern Slavery Act Transparency Statement|Sitemap|About US| Contact US: help@patsnap.com