Compensator for rotary working device of excavator
A technology of slewing compensation and working devices, which is applied to earth movers/excavators, construction, etc., to achieve low production costs, ensure coordination, adjust flexibility and adaptability
- Summary
- Abstract
- Description
- Claims
- Application Information
AI Technical Summary
Problems solved by technology
Method used
Image
Examples
Embodiment Construction
[0035] The present invention will be further described below in conjunction with the accompanying drawings. The following examples are only used to illustrate the technical solution of the present invention more clearly, but not to limit the protection scope of the present invention.
[0036] figure 1 Shown is a schematic diagram of the application of the compensator for the rotary working device in the present invention to the load-sensing multi-way valve. The schematic diagram includes: rotary reversing throttle valve 1, rotary compensator assembly 2, rotary compensator plunger assembly 3, rotary signal pressure reducing valve 4, on-off valve 5, check valve 6, orifice 7, boom The reversing throttle valve 8, the boom compensator spool 9, the boom signal pressure reducing valve 10, and the oil passages communicating with the above-mentioned various components. The oil circuit connection mode of the compensator hydraulic system for the rotary working device is as follows: the...
PUM
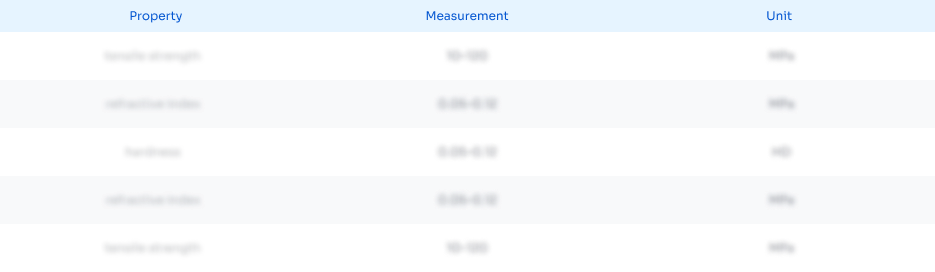
Abstract
Description
Claims
Application Information

- R&D Engineer
- R&D Manager
- IP Professional
- Industry Leading Data Capabilities
- Powerful AI technology
- Patent DNA Extraction
Browse by: Latest US Patents, China's latest patents, Technical Efficacy Thesaurus, Application Domain, Technology Topic, Popular Technical Reports.
© 2024 PatSnap. All rights reserved.Legal|Privacy policy|Modern Slavery Act Transparency Statement|Sitemap|About US| Contact US: help@patsnap.com