A friction-driven pushing robot
A pusher robot, friction-driven technology, applied in conveyor objects, animal feeding devices, loading/unloading, etc., can solve the problems of insufficient pushing capacity, large front resistance, and insufficient push, and improve cleaning and pushing. effect, improve the ability to push, reduce the effect of omission
- Summary
- Abstract
- Description
- Claims
- Application Information
AI Technical Summary
Problems solved by technology
Method used
Image
Examples
Embodiment 1
[0032] In a typical embodiment of the present invention, such as Figure 1-Figure 4 As shown, a friction-driven pushing robot is proposed.
[0033] Aiming at the problem that the current pusher robot is difficult to effectively push and stack loose and light feed, a friction-driven pusher robot is provided. The friction-driven rotating shell 1 is set to push and accumulate the feed. Surface to obtain friction to drive the rotating shell 1 to rotate, reduce the impact of feed contact cylinder friction on pushing efficiency, solve the problem of poor pushing efficiency of traditional pushing robots, and improve the ability to push scattered feed.
[0034] For the friction-driven pusher robot, it mainly includes a self-propelled platform, a rotating shell 1, a guide plate 2 and a lifting mechanism. The self-propelled platform is used as a whole mobile load-bearing structure, which drives the components installed on it to move as a whole, along the extension direction of the fence...
PUM
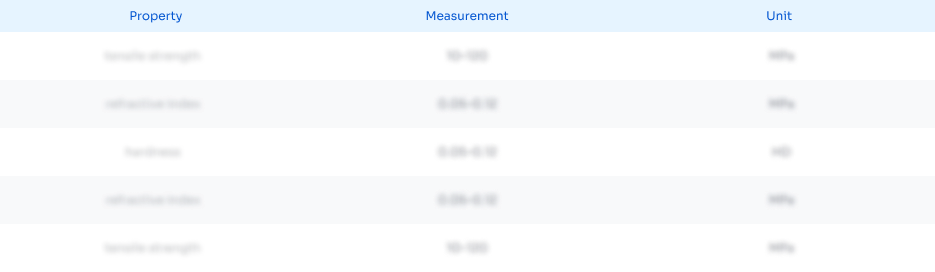
Abstract
Description
Claims
Application Information

- R&D
- Intellectual Property
- Life Sciences
- Materials
- Tech Scout
- Unparalleled Data Quality
- Higher Quality Content
- 60% Fewer Hallucinations
Browse by: Latest US Patents, China's latest patents, Technical Efficacy Thesaurus, Application Domain, Technology Topic, Popular Technical Reports.
© 2025 PatSnap. All rights reserved.Legal|Privacy policy|Modern Slavery Act Transparency Statement|Sitemap|About US| Contact US: help@patsnap.com