Large-load long-distance radiation-resistant high-precision snakelike arm
A long-distance, radiation-resistant technology, applied in the direction of program control manipulators, manufacturing tools, manipulators, etc., can solve the problems of complex motion control, low precision, small load capacity, etc., to reduce complexity, improve motion accuracy, and strong load. effect of ability
- Summary
- Abstract
- Description
- Claims
- Application Information
AI Technical Summary
Problems solved by technology
Method used
Image
Examples
Embodiment Construction
[0033] The following will clearly and completely describe the technical solutions in the embodiments of the present invention with reference to the accompanying drawings in the embodiments of the present invention. Obviously, the described embodiments are only some, not all, embodiments of the present invention. Based on the embodiments of the present invention, all other embodiments obtained by persons of ordinary skill in the art without making creative efforts belong to the protection scope of the present invention.
[0034] In the present invention, terms such as "mounting", "connecting", "connecting", "fixing", "front and rear", "left and right", "inside and outside", "up and down" should be interpreted in a broad sense based on the device, for example, " "Connection" can be a fixed connection, a detachable connection, or an integral connection; "connection" can be a direct connection or an indirect connection through an intermediary. Those of ordinary skill in the art ca...
PUM
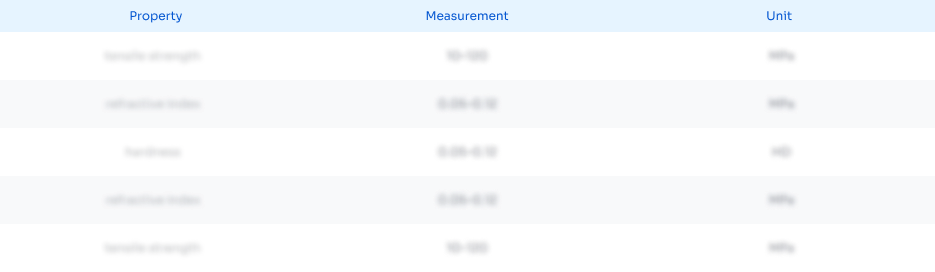
Abstract
Description
Claims
Application Information

- R&D
- Intellectual Property
- Life Sciences
- Materials
- Tech Scout
- Unparalleled Data Quality
- Higher Quality Content
- 60% Fewer Hallucinations
Browse by: Latest US Patents, China's latest patents, Technical Efficacy Thesaurus, Application Domain, Technology Topic, Popular Technical Reports.
© 2025 PatSnap. All rights reserved.Legal|Privacy policy|Modern Slavery Act Transparency Statement|Sitemap|About US| Contact US: help@patsnap.com