Three-coordinate curved surface compensation detection method for integral blade ring
A detection method, three-coordinate technology, applied in the direction of mechanical counter/curvature measurement, etc., can solve the problem of "offset" theoretical position of the measurement point, deviation of part leaf shape detection data, deviation of flow channel scanning, etc., to improve detection efficiency and accuracy, to ensure measurement accuracy, and to eliminate the effect of cosine error
- Summary
- Abstract
- Description
- Claims
- Application Information
AI Technical Summary
Problems solved by technology
Method used
Image
Examples
Embodiment Construction
[0038] The specific implementation manners of the present invention will be further described in detail below in conjunction with the accompanying drawings and embodiments. The following examples are used to illustrate the present invention, but are not intended to limit the scope of the present invention.
[0039] Such as Figure 4 As shown, the three-coordinate surface compensation detection method of the integral leaf ring in this embodiment is as follows.
[0040] Step 1: Align the overall leaf ring on the measuring turntable of the three-coordinate measuring instrument, and assemble the stylus according to the degree of distortion of the leaf shape, and inspect the assembled stylus and turntable;
[0041] Step 2: Process the NC model before measuring, and intercept the data points of the theoretical position and their vector directions on the NC model, such as Figure 5 , and segment the data points of the theoretical position of the leaf shape to determine the theoreti...
PUM
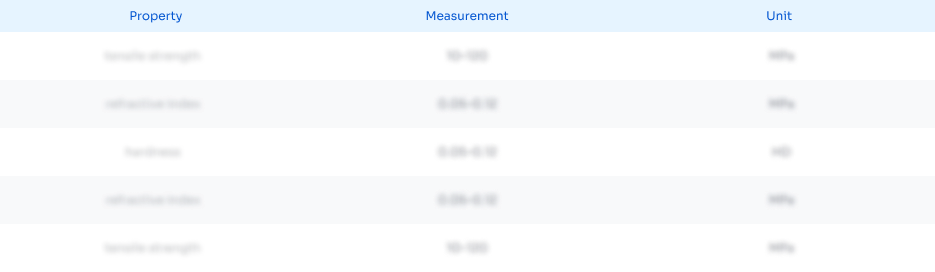
Abstract
Description
Claims
Application Information

- Generate Ideas
- Intellectual Property
- Life Sciences
- Materials
- Tech Scout
- Unparalleled Data Quality
- Higher Quality Content
- 60% Fewer Hallucinations
Browse by: Latest US Patents, China's latest patents, Technical Efficacy Thesaurus, Application Domain, Technology Topic, Popular Technical Reports.
© 2025 PatSnap. All rights reserved.Legal|Privacy policy|Modern Slavery Act Transparency Statement|Sitemap|About US| Contact US: help@patsnap.com