Defective workpiece sorting method and system for cutting-off machine
A technology for cutting machines and workpieces, which is applied in the field of sorting methods and systems for defective workpieces of cutting machines, which can solve the problems of increasing equipment cost and volume, inability to accurately judge defects, and inability to accurately judge when defective workpieces leave the cutting parts. , to achieve the effect of avoiding the reduction of detection accuracy, avoiding the reduction of result accuracy, and eliminating inaccurate data
- Summary
- Abstract
- Description
- Claims
- Application Information
AI Technical Summary
Problems solved by technology
Method used
Image
Examples
Embodiment Construction
[0045] In order to make the content of the present invention clearer and easier to understand, the content of the present invention will be further described below in conjunction with specific embodiments. Of course, the present invention is not limited to this specific embodiment, and general replacements known to those skilled in the art are also covered within the protection scope of the present invention.
[0046] Below in conjunction with specific embodiment and appended Figure 1~3 The present invention is described in further detail.
[0047] see figure 1 , the cutting machine defective workpiece sorting method in the present embodiment comprises:
[0048] Step 01: In the continuous state of the pulse signal, the workpiece moves from the cutting position to the conveyor belt, and the conveyor belt transports the workpiece to the sorting position; the detection position detects the first pulse segment where the front end and tail end of each workpiece pass through the ...
PUM
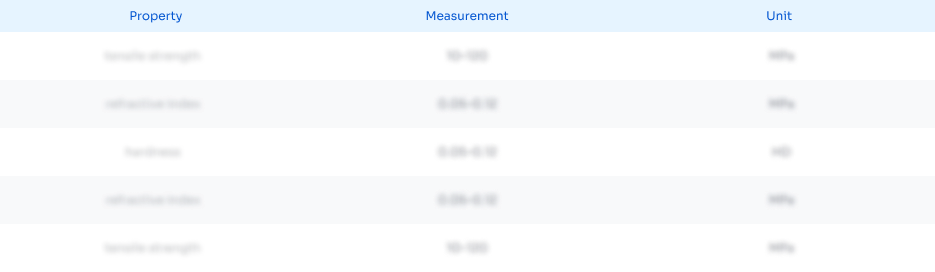
Abstract
Description
Claims
Application Information

- R&D
- Intellectual Property
- Life Sciences
- Materials
- Tech Scout
- Unparalleled Data Quality
- Higher Quality Content
- 60% Fewer Hallucinations
Browse by: Latest US Patents, China's latest patents, Technical Efficacy Thesaurus, Application Domain, Technology Topic, Popular Technical Reports.
© 2025 PatSnap. All rights reserved.Legal|Privacy policy|Modern Slavery Act Transparency Statement|Sitemap|About US| Contact US: help@patsnap.com