Micro-torque rotation angle sensor and deflection angle testing method thereof
A sensor and micro-torque technology, applied in the field of inertial instruments, can solve problems such as disturbance torque, zero position offset, and unsatisfactory symmetry, and achieve the effects of reducing disturbance torque, ensuring electrical insulation reliability, and avoiding disturbance torque
- Summary
- Abstract
- Description
- Claims
- Application Information
AI Technical Summary
Problems solved by technology
Method used
Image
Examples
Embodiment Construction
[0033] Embodiments of the present invention are described in further detail below in conjunction with the accompanying drawings:
[0034] A micro-torque angle sensor, such as figure 1 As shown, it includes a stator core 1 , an output winding 2 , an excitation winding 3 , a rotor 4 and a magnetic permeable ring 5 .
[0035] The stator core 1 is installed on the fixed assembly of the gyroscope; on the annular inner wall of the stator core 1, an output winding 2 and an excitation winding 3 are installed at intervals; on the side near the axis of the output winding 2 and the excitation winding 3 The rotor is coaxially installed, and the rotor 4 is a short-circuit ring window structure, which is installed on the floating assembly of the gyroscope, and its physical position is set concentrically with the stator core 1 during operation; multiple windows are equidistant on the side wall of the rotor , the longitudinal working side 6 of the window is respectively aligned with the midl...
PUM
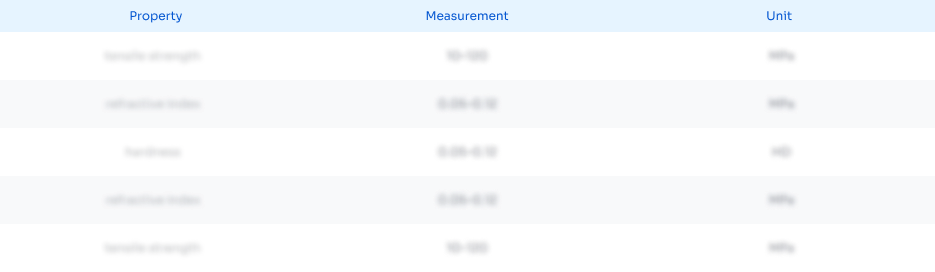
Abstract
Description
Claims
Application Information

- R&D Engineer
- R&D Manager
- IP Professional
- Industry Leading Data Capabilities
- Powerful AI technology
- Patent DNA Extraction
Browse by: Latest US Patents, China's latest patents, Technical Efficacy Thesaurus, Application Domain, Technology Topic, Popular Technical Reports.
© 2024 PatSnap. All rights reserved.Legal|Privacy policy|Modern Slavery Act Transparency Statement|Sitemap|About US| Contact US: help@patsnap.com