Method and device for detecting joint rigidity of robot and robot
A detection device and detection method technology, applied in the field of robots, can solve problems such as difficulty in determining whether the stiffness of robot joints meets design requirements, etc.
- Summary
- Abstract
- Description
- Claims
- Application Information
AI Technical Summary
Problems solved by technology
Method used
Image
Examples
Embodiment 1
[0060] In this embodiment, the above-mentioned robot includes a joint and a mechanical arm, one end of the above-mentioned mechanical arm is connected to the above-mentioned joint, the other end of the above-mentioned mechanical arm is used to clamp a load, the quality of the load is 175kg, and the detection method of the joint stiffness of the robot includes the following step:
[0061] Control the above-mentioned mechanical arm to grab the above-mentioned load, and control the above-mentioned joint to rotate to a horizontal state, and detect the current position of any point on the above-mentioned mechanical arm and the position of the rotation center of the above-mentioned joint, and obtain the first position A' and the second position O respectively ', the coordinates of the first position A' in the vertical plane are (924.544, 193.8307), and the coordinates of the second position O' in the vertical plane are (62.114, -169.16);
[0062] Control the above-mentioned mechanic...
PUM
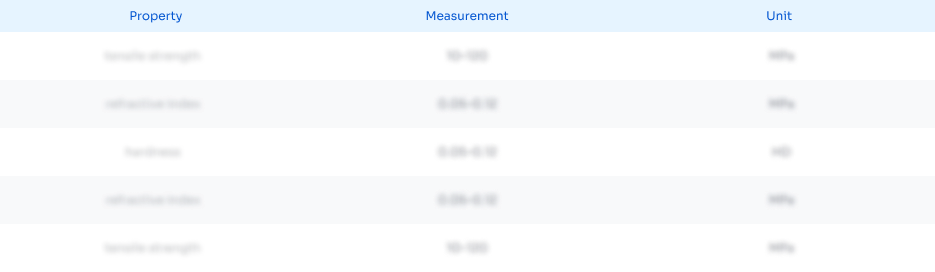
Abstract
Description
Claims
Application Information

- Generate Ideas
- Intellectual Property
- Life Sciences
- Materials
- Tech Scout
- Unparalleled Data Quality
- Higher Quality Content
- 60% Fewer Hallucinations
Browse by: Latest US Patents, China's latest patents, Technical Efficacy Thesaurus, Application Domain, Technology Topic, Popular Technical Reports.
© 2025 PatSnap. All rights reserved.Legal|Privacy policy|Modern Slavery Act Transparency Statement|Sitemap|About US| Contact US: help@patsnap.com