Vibration isolator based on hydraulic servo control
A technology of servo control and vibration isolator, which is applied in the field of vibration reduction and noise reduction, can solve the problems that the metal spring vibration isolator cannot satisfy, the vibration source excitation constant force component has a large variation range, and achieve the effect of ensuring support and avoiding damage
- Summary
- Abstract
- Description
- Claims
- Application Information
AI Technical Summary
Problems solved by technology
Method used
Image
Examples
Embodiment Construction
[0022] In order to have a clearer understanding of the technical features, purposes and effects of the present invention, the specific implementation manners of the present invention will now be described in detail with reference to the accompanying drawings.
[0023] Such as figure 1 As shown, a vibration isolator based on hydraulic servo control provided by an embodiment of the present invention includes a vibration isolation element 1 , an integrated valve block 2 and a control box 3 . The vibration isolation element 1 is installed between the vibration source and the controlled object. The vibration isolation element 1 includes a cylinder body 14, a spring 15, a piston 16, a front end cover 12, a rear end cover 18, a thrust support block 11, a spring pressing cap 13, a magnetic Ring 111, magnetic ring fixing device, displacement sensor 19. The front end cover 12 and the rear end cover 18 are fixedly installed at both ends of the cylinder body 14 . The rear end of the spr...
PUM
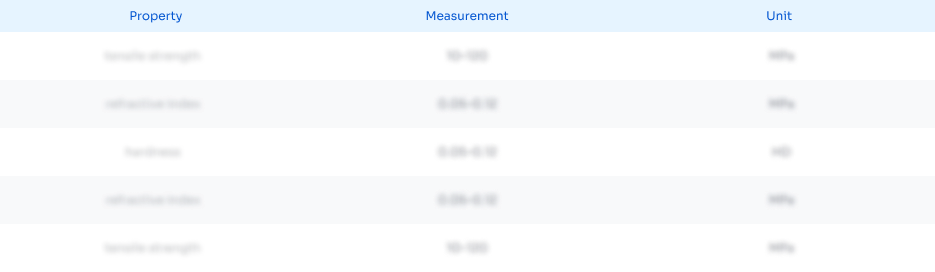
Abstract
Description
Claims
Application Information

- R&D
- Intellectual Property
- Life Sciences
- Materials
- Tech Scout
- Unparalleled Data Quality
- Higher Quality Content
- 60% Fewer Hallucinations
Browse by: Latest US Patents, China's latest patents, Technical Efficacy Thesaurus, Application Domain, Technology Topic, Popular Technical Reports.
© 2025 PatSnap. All rights reserved.Legal|Privacy policy|Modern Slavery Act Transparency Statement|Sitemap|About US| Contact US: help@patsnap.com