Solar heliostat aeroelastic model and design method thereof
An aeroelastic model and design method technology, applied in aerodynamic tests, measuring devices, instruments, etc., can solve problems such as inapplicability, achieve the effects of simplifying production, ensuring integrity, and reducing welding points
- Summary
- Abstract
- Description
- Claims
- Application Information
AI Technical Summary
Problems solved by technology
Method used
Image
Examples
Embodiment
[0053] like Figure 1-Figure 2 As shown, an aeroelastic model of a solar heliostat of the present invention includes a mirror panel 4, a plane purlin 1, a support truss 2, a torsion-resistant steel beam 3 and a column 5, and the plane purlin 1 is fixed below the mirror panel 4, and the plane Purlins 1 are fixed at intervals to support trusses 2 , torsion-resistant steel beams 3 run through the fixed support trusses 2 , and torsion-resistant steel beams 3 are placed on the top of columns 5 .
[0054] In this embodiment, the top of the column 5 is also fixedly welded with a connecting device 6. The connecting device 6 includes a supporting plate 61 and a cover plate 62. The supporting plate 61 is fixed on the top of the column 5. Groove, the through groove of supporting plate 61 and cover plate 62 can be combined to form the through hole that accommodates torsion-resistant steel beam 3, and the bottom end of column 5 is fixedly welded with chassis 7, and chassis 7 is provided wi...
PUM
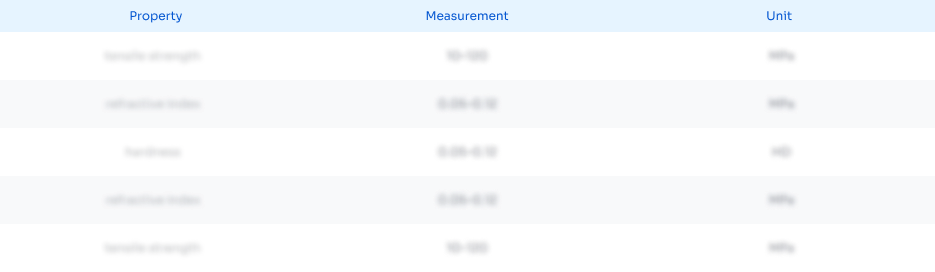
Abstract
Description
Claims
Application Information

- R&D Engineer
- R&D Manager
- IP Professional
- Industry Leading Data Capabilities
- Powerful AI technology
- Patent DNA Extraction
Browse by: Latest US Patents, China's latest patents, Technical Efficacy Thesaurus, Application Domain, Technology Topic, Popular Technical Reports.
© 2024 PatSnap. All rights reserved.Legal|Privacy policy|Modern Slavery Act Transparency Statement|Sitemap|About US| Contact US: help@patsnap.com