Self-balancing container
A self-balancing, container technology, applied in the field of containers, can solve the problems of no buffer function and damaged goods, and achieve the effect of enhancing the magnetic field force
- Summary
- Abstract
- Description
- Claims
- Application Information
AI Technical Summary
Problems solved by technology
Method used
Image
Examples
Embodiment 1
[0019] Such as figure 1 As shown, a self-balancing container includes an outer box body 1, an inner box body 11 is movably installed in the inner cavity of the outer box body 1, and a braking mechanism 2 is fixedly installed in the inner cavity of the outer box body 1, and the braking mechanism 2 Including the top base 201, the bottom surface of the top base 201 is fixedly connected with a steel cable 202, the end of the steel cable 202 away from the top base 201 is fixedly connected with a base 203, the top surface of the inner box 11 is fixedly installed with a buffer 204, and the buffer 204 A number of buffer balls 205 are movable in the inner cavity, piezoelectric ceramics 206 are fixedly installed on the top surface of the inner cavity of the inner box body 11, and several turn groups 207 are uniformly wound on the surface of the inner box body 11, and the inner cavity of the outer box body 1 The bottom surface is filled with fine sand 208, and the side of the inner cavit...
Embodiment 2
[0027] Such as figure 2 As shown, the difference between this embodiment and Embodiment 1 is: the bottom surface of the inner box body 11 is evenly distributed and fixedly connected with several steel rods 210, the top surface of the inner cavity of the outer box body 1 is fixedly equipped with slide rails 211, and the steel rods The end of 210 away from the bottom surface of the inner box 11 is slidably socketed on the top surface of the slide rail 211, and the top of the steel rod 210 is electrically connected with the line group 207, so that when the inner box 11 performs emergency braking, the steel rod 210 can The surface of the slide rail 211 slides, thereby cutting the magnetic induction lines and generating induced currents;
[0028] And the magnitude of the induced electromotive force in the circuit is proportional to the magnitude of the induced electromotive force in the circuit and the rate of change of the magnetic flux passing through this circuit, that is If ...
PUM
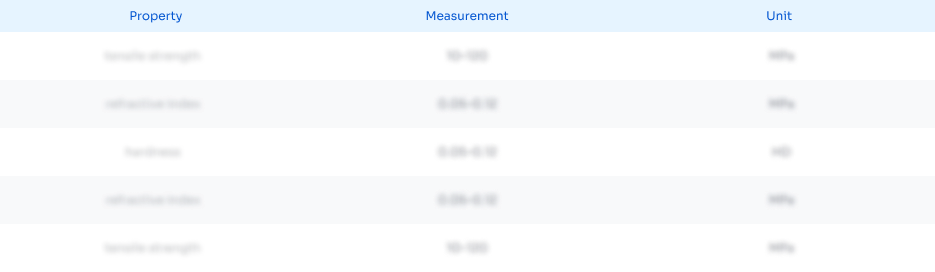
Abstract
Description
Claims
Application Information

- R&D
- Intellectual Property
- Life Sciences
- Materials
- Tech Scout
- Unparalleled Data Quality
- Higher Quality Content
- 60% Fewer Hallucinations
Browse by: Latest US Patents, China's latest patents, Technical Efficacy Thesaurus, Application Domain, Technology Topic, Popular Technical Reports.
© 2025 PatSnap. All rights reserved.Legal|Privacy policy|Modern Slavery Act Transparency Statement|Sitemap|About US| Contact US: help@patsnap.com