Automatic adjustment frame precision detection device and frame detection reference determination method
A precision detection and automatic adjustment technology, applied in the direction of measuring devices, mechanical measuring devices, mechanical devices, etc., can solve the inconvenience of frame precision adjustment and vehicle problem analysis, and many welds at the joint between the flange of the lower swing arm and the longitudinal beam , Can not truly reflect the welding accuracy of the frame and other issues, to achieve the effect of eliminating the difficulty of position adjustment, low cost, and lightweight design
- Summary
- Abstract
- Description
- Claims
- Application Information
AI Technical Summary
Problems solved by technology
Method used
Image
Examples
Embodiment Construction
[0035] The specific implementation manners of the present invention will be described in detail below in conjunction with the accompanying drawings.
[0036] like Figure 1 to Figure 8 As shown, the automatic adjustment frame accuracy detection device of this embodiment includes a front base 1 , a middle base 2 and a rear base 3 arranged in sequence along the front and rear directions of the frame.
[0037] The left / right fixed support block 4 / 5 and the middle adjustment locator 6 on the rear base 3, the adjustment locator 6 is composed of an adjustment guide rail 7, a fixed pin seat 8 and a positioning pin 9, and the positioning pin 9 is installed on the fixed pin On the seat 8, the fixed pin seat 8 is slidably connected on the adjustment guide rail 7, and the adjustment guide rail 7 is installed on the rear base 3 along the front-rear direction.
[0038] The middle base 2 is symmetrically provided with a left / right adjustment mechanism, and the left / right adjustment mechani...
PUM
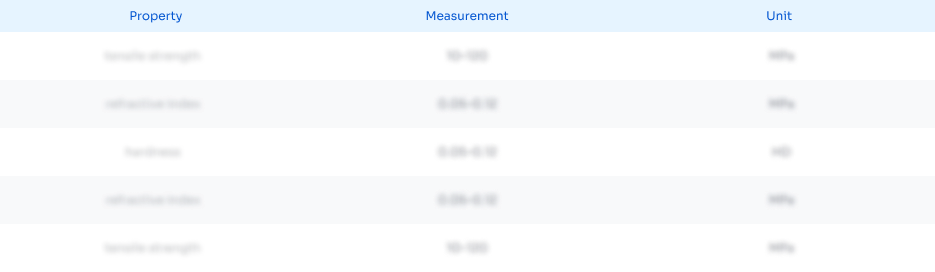
Abstract
Description
Claims
Application Information

- R&D
- Intellectual Property
- Life Sciences
- Materials
- Tech Scout
- Unparalleled Data Quality
- Higher Quality Content
- 60% Fewer Hallucinations
Browse by: Latest US Patents, China's latest patents, Technical Efficacy Thesaurus, Application Domain, Technology Topic, Popular Technical Reports.
© 2025 PatSnap. All rights reserved.Legal|Privacy policy|Modern Slavery Act Transparency Statement|Sitemap|About US| Contact US: help@patsnap.com