Pressure-displacement cooperative control stationary shoulder friction stir welding spindle head device
A friction stir welding and static shoulder technology, which is applied in welding equipment, manufacturing tools, non-electric welding equipment, etc., can solve problems such as unstable welding process, achieve compact structure, stable static process, and improve rigidity and stability.
- Summary
- Abstract
- Description
- Claims
- Application Information
AI Technical Summary
Problems solved by technology
Method used
Image
Examples
Embodiment 1
[0027] A pressure-displacement cooperative control static shoulder friction stir welding spindle head device, including a clamping system, a hydraulic system and a static shoulder system,
[0028] The clamping system includes a housing 6, a rotating shaft 7, a knife handle 10 and a stirring needle 1. The housing 6 adopts a hollow structure, and the rotating shaft 7 is arranged in the housing 6 through a bearing group 8. The first end of pin 1 is connected;
[0029] The hydraulic system includes an outer piston 5, an oil chamber 12 and an oil seal cover 11. The outer piston 5 is connected with the lower part of the housing 6 through a guide key. The outer piston 5 moves up and down along the outer wall of the housing 6. The oil seal cover 11 and the tail of the housing 6 The ends are fixedly connected, the oil seal cover 11 adopts a hollow structure, and an oil chamber 12 is formed between the outer piston 5, the housing 6 and the oil seal cover 11, and the oil chamber 12 is us...
Embodiment 2
[0032] On the basis of Embodiment 1, the spindle head device also includes a support frame 17 and a displacement sensor 18. The head end of the support frame 17 is fixedly connected to the outside of the housing 6, and the tail end of the support frame 17 is connected to the displacement sensor 18. The displacement sensor 18 is used to detect the plate thickness change of the workpiece 16 to be welded in real time and send the data to the control system for real-time adjustment, and the control system then controls the hydraulic system to adjust its output pressure, that is, the outer piston 5 moves to drive the stationary shoulder system to move, In order to achieve the purpose of real-time control of the axial displacement of the stirring needle 1.
Embodiment 3
[0034] On the basis of Embodiment 2, the number of bearing groups 8 is 2 groups, and the bearing groups 8 are respectively arranged in groups along the rotating shaft 7 from top to bottom. The lower bearing set 8 has four bearings.
[0035] The bearing adopts angular contact bearing.
[0036] An outer spacer 13 and an inner spacer 14 are sequentially arranged between adjacent bearings, and a tight locking nut 9 for fixing the bearing is arranged at the rear end of the rearmost bearing.
PUM
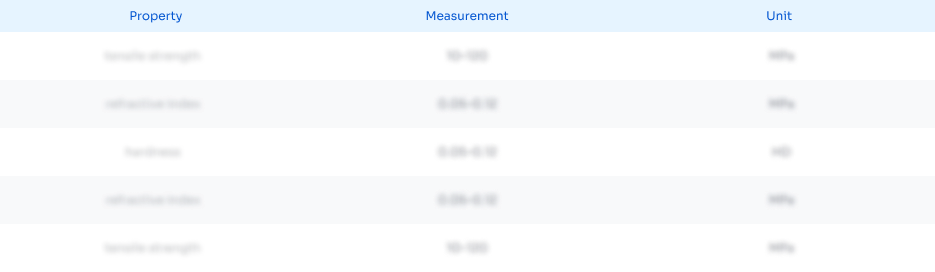
Abstract
Description
Claims
Application Information

- Generate Ideas
- Intellectual Property
- Life Sciences
- Materials
- Tech Scout
- Unparalleled Data Quality
- Higher Quality Content
- 60% Fewer Hallucinations
Browse by: Latest US Patents, China's latest patents, Technical Efficacy Thesaurus, Application Domain, Technology Topic, Popular Technical Reports.
© 2025 PatSnap. All rights reserved.Legal|Privacy policy|Modern Slavery Act Transparency Statement|Sitemap|About US| Contact US: help@patsnap.com