A topology and method for mutual correction of dual motor current sensors
A current sensor and mutual correction technology, applied in the current controller, motor parameter estimation/correction, motor control and other directions, can solve problems such as increased cost and sampling point limitation, achieve cost saving, fast correction speed, easy data The effect of sampling
- Summary
- Abstract
- Description
- Claims
- Application Information
AI Technical Summary
Problems solved by technology
Method used
Image
Examples
Embodiment Construction
[0049] Simulate the situation where the current sensor produces errors, introducing errors to the six current sensors: f A1 =0.1, f B1 =0.2, f C1 =-0.1, f A2 =-0.05, f B2 =0.1, f C2 =-0.2, k A1 =1.2, k B1 =0.9, k C1 =1.1, k A2 =1.05, k B2 =1.15, k C2 = 0.9. At this point, the system is calibrated, and the specific steps are as follows:
[0050] Step 1: Follow as figure 1 According to the topology wiring, sampling is performed at the initial stage of the control cycle of the five-segment SVPWM control algorithm, and the feedback results of each phase current of the dual-motor subsystem are calculated in combination with formula (1). The results are fed back to form a closed loop to control the operation of the motor.
[0051] Step 2: Generate figure 2 For the PWM correction signal shown, the position of the sampling point of the feedback current in this period does not change, and the feedback current can be obtained by formula (2). The five-stage SVPWM control ...
PUM
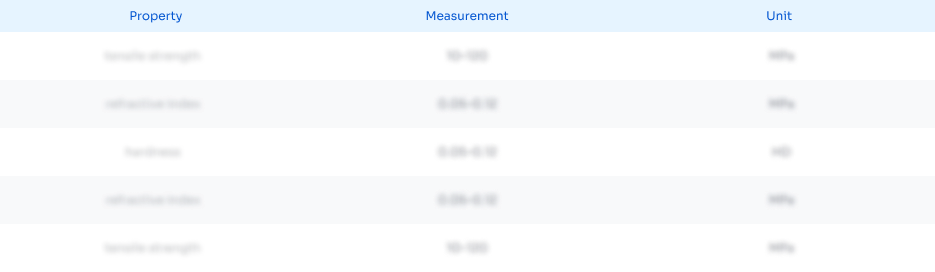
Abstract
Description
Claims
Application Information

- R&D
- Intellectual Property
- Life Sciences
- Materials
- Tech Scout
- Unparalleled Data Quality
- Higher Quality Content
- 60% Fewer Hallucinations
Browse by: Latest US Patents, China's latest patents, Technical Efficacy Thesaurus, Application Domain, Technology Topic, Popular Technical Reports.
© 2025 PatSnap. All rights reserved.Legal|Privacy policy|Modern Slavery Act Transparency Statement|Sitemap|About US| Contact US: help@patsnap.com