Slurry balance pipe jacking construction method
A mud-water balance and construction method technology, applied in pipeline laying and maintenance, pipes/pipe joints/fittings, mechanical equipment, etc., can solve problems such as poor results, and achieve the effect of reducing jacking force and friction
- Summary
- Abstract
- Description
- Claims
- Application Information
AI Technical Summary
Problems solved by technology
Method used
Image
Examples
Embodiment 1
[0032] This embodiment provides a mud-water balance pipe jacking construction method, and the mud-water balance pipe jacking includes a plurality of pipe joints, such as figure 1 As shown, the method includes the following steps:
[0033] S1: Stir the drag reducing mud on the ground; the drag reducing mud includes bentonite, soda ash, sodium carboxymethylcellulose and water, bentonite is 17% by weight, soda ash is 1% by weight, sodium carboxymethylcellulose is 0.3% by weight, and water is wt81.7%;
[0034] S2: Soak water in drag-reducing mud;
[0035] S3: The drag reducing mud is pumped between the outer wall of the pipe joint 1 and the soil, and a mud ring is formed around the pipe joint 1;
[0036] S4: The first pipe section 1 is jacked in, and when it is in place, stop grouting and remove the first pipe section 1;
[0037] S5: install the next pipe section 1 between the first pipe section 1 and the roadheader, inject grout and jacking;
[0038] S6: Cycle S3-S5 until the...
Embodiment 2
[0046] This embodiment provides a mud-water balance pipe jacking construction method. The difference from Embodiment 1 is that bentonite is wt13%, soda ash is wt0.5%, sodium carboxymethylcellulose is wt0.1%, and water is wt86. 4%.
Embodiment 3
[0048]This embodiment provides a mud-water balance pipe jacking construction method. The difference from Embodiment 1 and Embodiment 2 is that bentonite is wt15%, soda ash is wt0.8%, and sodium carboxymethylcellulose is wt0.2%. Water is wt84%.
[0049] The following table has provided the relationship between the slurry proportioning and the coefficient of friction in Embodiment 1, Embodiment 2, Embodiment 3 and other situations, as can be seen from it, bentonite is 13wt%-17wt%, and soda ash is 0.5wt%- 1 wt%, sodium carboxymethyl cellulose 0.1 wt%-0.3 wt%, and the balance being water, the drag reduction effect is better.
[0050] Serum ratio
[0051]
[0052]
PUM
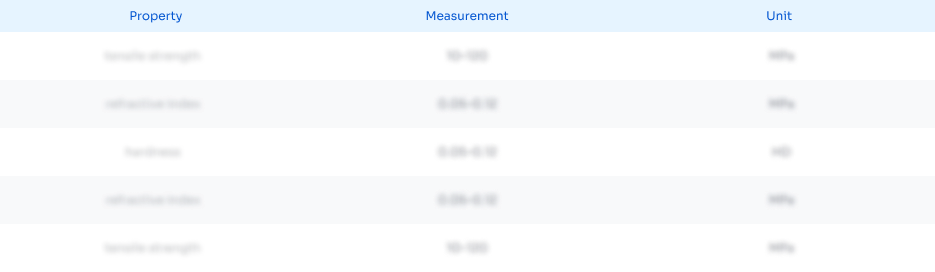
Abstract
Description
Claims
Application Information

- Generate Ideas
- Intellectual Property
- Life Sciences
- Materials
- Tech Scout
- Unparalleled Data Quality
- Higher Quality Content
- 60% Fewer Hallucinations
Browse by: Latest US Patents, China's latest patents, Technical Efficacy Thesaurus, Application Domain, Technology Topic, Popular Technical Reports.
© 2025 PatSnap. All rights reserved.Legal|Privacy policy|Modern Slavery Act Transparency Statement|Sitemap|About US| Contact US: help@patsnap.com