A composite empennage based on h-shaped spar reinforcement, manufacturing method and molding die
A technology of composite materials and forming molds, which is applied in the aviation field, can solve the problems of aircraft structure weight reduction, empennage assembly coordination route complexity, and cost increase, so as to optimize the force transmission route, reduce initial and repeated costs, and improve the yield rate Effect
- Summary
- Abstract
- Description
- Claims
- Application Information
AI Technical Summary
Problems solved by technology
Method used
Image
Examples
Embodiment 1
[0031] Such as figure 1 As shown, this embodiment provides a composite material integral empennage based on H-shaped spar reinforcement. The integral empennage adopts a wing-body fusion design scheme, and the fuselage shell is designed as a composite material wing-body integrated structure, and its interior adopts an H-shaped wing Beam reinforcement, the integral empennage and the H-shaped spar take the chord line of the empennage airfoil as the separation surface, and are divided into two parts, the wing body integrated empennage panel with cap ribs.
[0032] Further, the H-shaped spar includes a spar shell and a sandwich layer, and the spar shell includes a vertically symmetrical rib structure with caps in the empennage section, and its cross-sectional shape is an H-shaped structure; It is the upper half and the lower half. The upper half and the lower half are both C-shaped rib structures with caps. The space between the spar shell and the outer skin is filled with a sandwi...
Embodiment 2
[0038] The present application also provides the above-mentioned manufacturing method based on the composite empennage reinforced by the H-shaped spar, the manufacturing method comprising the following steps:
[0039] First, lay the layers of the panel skin in the above-mentioned mold body, lay the layers of the spar shell in the spar block assembly and complete the filling and repair of the foam sandwich layer. Block assemblies with layup and core are positioned together on the mold body and assembled with fasteners;
[0040] Then, remove the connecting bolts and lock nuts of the spar block assembly to ensure that the empennage section block and the fuselage section block are in a free state, and complete the co-curing of the wing-body empennage panel after bag sealing forming;
[0041] Finally, in the closing mould, the wing-body-integrated empennage panel is glued along the separation surface to form an integral empennage.
[0042] Based on the design idea of integrated...
Embodiment 3
[0044] The present embodiment provides the forming mold of the aforementioned integral empennage body panel, such as Figure 5 , Image 6 As shown, the forming mold is composed of a mold body and a spar block assembly. The mold body is used for forming the skin of the wing body and empennage. The spar block assembly is installed in the mold body through fasteners. The spar blocks are used for the layup and co-curing of the spar shells, and are divided into blocks in the wing root area according to the structural characteristics of the spar, and are divided into empennage section blocks and fuselage section blocks. The fuselage block is connected by a quick-release structure to form a wing spar block assembly.
[0045] The aforementioned quick-release structure of the spar block is composed of a connecting seat and a connecting block, the connecting seat is connected with the spar block of the empennage section with a fastener, and the connecting block is connected with the spar...
PUM
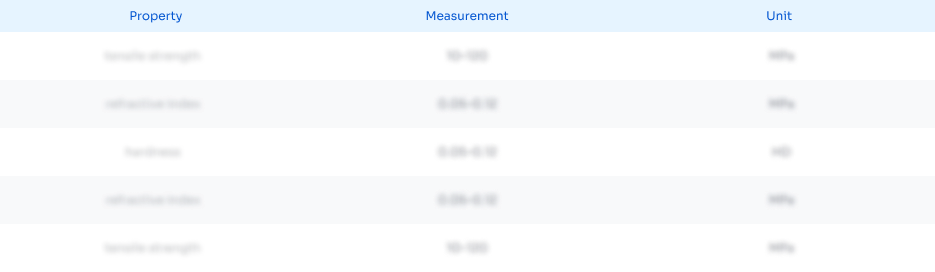
Abstract
Description
Claims
Application Information

- R&D
- Intellectual Property
- Life Sciences
- Materials
- Tech Scout
- Unparalleled Data Quality
- Higher Quality Content
- 60% Fewer Hallucinations
Browse by: Latest US Patents, China's latest patents, Technical Efficacy Thesaurus, Application Domain, Technology Topic, Popular Technical Reports.
© 2025 PatSnap. All rights reserved.Legal|Privacy policy|Modern Slavery Act Transparency Statement|Sitemap|About US| Contact US: help@patsnap.com