Method for obtaining high-precision hardening model parameters of material in complex stress state
A technology of model parameters and complex stress, applied in the direction of applying stable tension/pressure to test the strength of materials, analyzing materials, computer materials science, etc., can solve the problems of not taking into account the characterization of material properties at the same time, and achieve good application results
- Summary
- Abstract
- Description
- Claims
- Application Information
AI Technical Summary
Problems solved by technology
Method used
Image
Examples
Embodiment 1
[0070] Material samples such as Figure 9 - Figure 13 Shown:
[0071] Uniaxial tensile specimen: The uniaxial tensile specimen has a clear national standard for specimen size, and the triaxiality of the material element stress in the main deformation area during the stress process is 0.333.
[0072] Pure shear specimen: The stress triaxiality of the unit in the main deformation area of the pure shear specimen remains at about 0 during the test.
[0073] Tensile specimen with central hole: the stress triaxiality of tensile specimen with central hole is 0.33-0.4.
[0074] Notched tensile specimens: For specimens between uniaxial and biaxial tensile, the stress triaxiality changes between 0.4-0.577, and different notched specimens can well describe this stress situation.
[0075] The true stress and true strain curve of the material sample is obtained by using the traditional uniaxial tensile test method, and then the existing hardening model is used to fit the epitaxy comb...
PUM
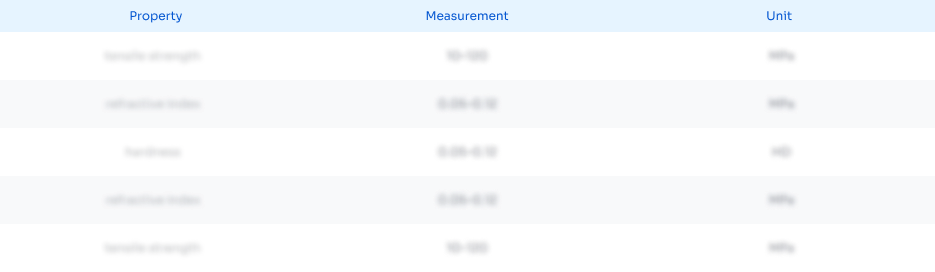
Abstract
Description
Claims
Application Information

- R&D Engineer
- R&D Manager
- IP Professional
- Industry Leading Data Capabilities
- Powerful AI technology
- Patent DNA Extraction
Browse by: Latest US Patents, China's latest patents, Technical Efficacy Thesaurus, Application Domain, Technology Topic, Popular Technical Reports.
© 2024 PatSnap. All rights reserved.Legal|Privacy policy|Modern Slavery Act Transparency Statement|Sitemap|About US| Contact US: help@patsnap.com