Single-pile offshore floating fan vibration reduction control structure
A control structure, floating technology, applied in the direction of vibration suppression adjustment, non-rotation vibration suppression, installation/support of wind turbine configuration, etc. Increase the overall cost of floating fans and other issues
- Summary
- Abstract
- Description
- Claims
- Application Information
AI Technical Summary
Problems solved by technology
Method used
Image
Examples
Embodiment
[0031] Such as Figure 1-4 As shown, the present invention provides a single-pile offshore floating wind turbine vibration reduction control structure, including a tuned mass damper 14, a lattice steel truss 1, an outer ring steel truss 13, steel strands 3, steel supports and protective devices, The lattice steel truss 1 is connected to the outside of the foundation platform 7 of the floating wind turbine, and its lower part is provided with a lattice steel truss steel support 6, and the four lattice steel trusses 1 are connected by ring steel trusses 13 to form a whole, and each lattice steel truss 1 The tuning mass damper 14 connected to the foundation platform 7 of the floating wind turbine is installed inside, the tower frame 8 of the floating wind turbine and the lattice steel truss 1 are connected through the steel strand 3, and the steel support 12 of the ring steel truss is connected to the foundation platform 7 of the floating wind turbine and External ring steel trus...
PUM
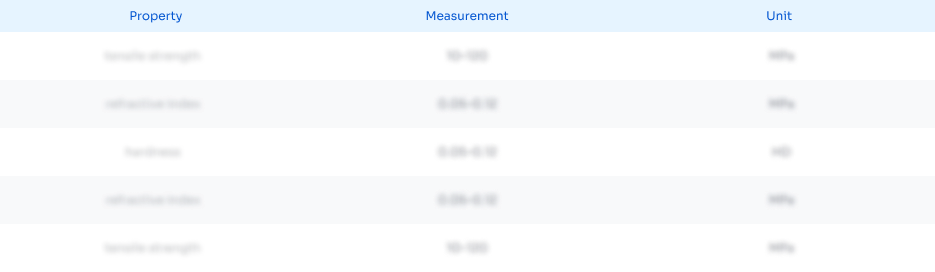
Abstract
Description
Claims
Application Information

- R&D
- Intellectual Property
- Life Sciences
- Materials
- Tech Scout
- Unparalleled Data Quality
- Higher Quality Content
- 60% Fewer Hallucinations
Browse by: Latest US Patents, China's latest patents, Technical Efficacy Thesaurus, Application Domain, Technology Topic, Popular Technical Reports.
© 2025 PatSnap. All rights reserved.Legal|Privacy policy|Modern Slavery Act Transparency Statement|Sitemap|About US| Contact US: help@patsnap.com