Special equipment for welding steel components
A special device and component technology, which is applied in the field of special welding devices for section steel components, can solve the problems of reducing the work efficiency of operators, prone to bumps, and increasing the work process of operators, so as to improve operability and convenience, improve positioning effectiveness, The effect of increasing flexibility
- Summary
- Abstract
- Description
- Claims
- Application Information
AI Technical Summary
Problems solved by technology
Method used
Image
Examples
Embodiment 1
[0039] Example 1, such as Figure 1-2 As shown, during the welding work of the section steel, the servo motor B11 can be started through the console 4 to drive the driving gear 12 to rotate, forcing the driving gear 12 and the driven gear 10 to mesh with each other to drive the rotating column 9 to rotate as a whole, and prompting the rotating column 9 to drive the fixed plate 2. Under the cooperation of the ring guide rail and the guide block, it rotates around, and then adjusts the angle of the fixed plate 2 as a whole, and changes the position of the welded steel on the fixed plate 2. The operator can adjust the position suitable for the operation, which is convenient for the operator to observe. , to increase the flexibility of device use.
Embodiment 2
[0040] Example 2, such as Figure 1-2 As shown, after the welding of one side of the web and the flange plate is completed, the servo motor A3 and the rotating motor 7 can be started through the console 4, and the two-way screw rod A14 is driven to rotate by the start of the servo motor A3, and the two-way screw rod A14 The rotation of the two groups of internally threaded tubes A13 is driven away from each other, and drives the hinged support plate 8 to move and expand, forcing the hinged support plate 8 to lift the annular chute 703 under the cooperation of the guide block 705 and the guide plate 702. At this time, the The start of the rotating motor 7 drives the connecting frame to rotate 180° under the sliding of the slider 701 and the annular chute 703, turning over the H-shaped steel as a whole, and then turning over the servo motor A3 to allow the hinged support plate 8 to be accommodated, and clamping the H-shaped steel again , to perform welding operation on the other...
Embodiment 3
[0041] Example 3, such as Figure 4 As shown, during welding when the welding torch 19 moves horizontally under the cooperation of the electromagnetic guide rail 21 and the electromagnetic guide block 20, the suction fan 17 can be started through the console 4, and the telescopic tube 172 and the flow guide tube 173 of the suction fan 17 in the telescopic state can be used. Under the connection and cooperation, the slag inclusions and dust that appear in the welding of the welding torch 19 are absorbed under the corresponding suction port 174, so that the residue is automatically collected into the collection tank 171, with subsequent cleaning, the automatic dust collection effect of the welding work of the device is increased, and the welding process is improved. Accuracy and convenience of follow-up cleaning work.
[0042] Working principle: when the device is in use, first place the web flat on the bearing of the positioning platform 16, and use the console 4 to start the e...
PUM
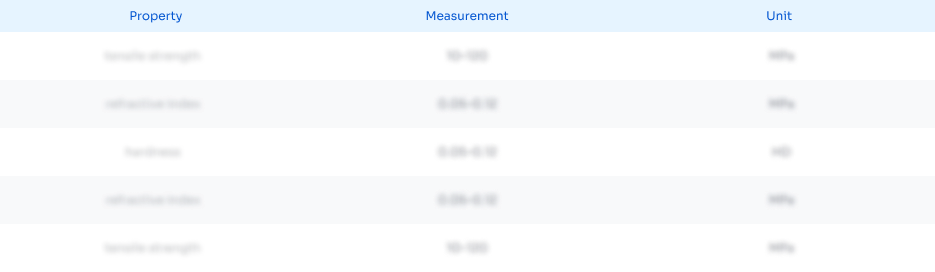
Abstract
Description
Claims
Application Information

- Generate Ideas
- Intellectual Property
- Life Sciences
- Materials
- Tech Scout
- Unparalleled Data Quality
- Higher Quality Content
- 60% Fewer Hallucinations
Browse by: Latest US Patents, China's latest patents, Technical Efficacy Thesaurus, Application Domain, Technology Topic, Popular Technical Reports.
© 2025 PatSnap. All rights reserved.Legal|Privacy policy|Modern Slavery Act Transparency Statement|Sitemap|About US| Contact US: help@patsnap.com