Composite plastic pipe production system and using method thereof
A production system and technology for plastic pipes, applied in the field of composite plastic pipe production equipment, can solve the problems of plastic pipe bending diameter, waste of time, inability to produce composite plastic pipes, etc.
- Summary
- Abstract
- Description
- Claims
- Application Information
AI Technical Summary
Problems solved by technology
Method used
Image
Examples
Embodiment Construction
[0029] In order to make the technical means, technical features, invention objectives and technical effects realized by the present invention easy to understand, the present invention will be further described below in conjunction with specific illustrations.
[0030] Such as figure 1 - As shown in -4, a kind of composite plastic pipe production system provided by the present invention comprises extruding mechanism 1, winding mechanism 2, heating mechanism 3, traction mechanism 5 arranged in sequence; winding mechanism 2 and traction mechanism 5 are located at slide rail 4 Above, the extruding mechanism 1 is used to produce the plastic pipe 6, the winding mechanism 2 is used to wrap the protective tape on the plastic pipe 6, and the heating mechanism 3 is used to carry out Heating, so that the protective belt and the plastic pipe 6 are bonded together to form a composite plastic pipe, and the traction mechanism 5 is used to pull the composite plastic pipe to move forward;
[...
PUM
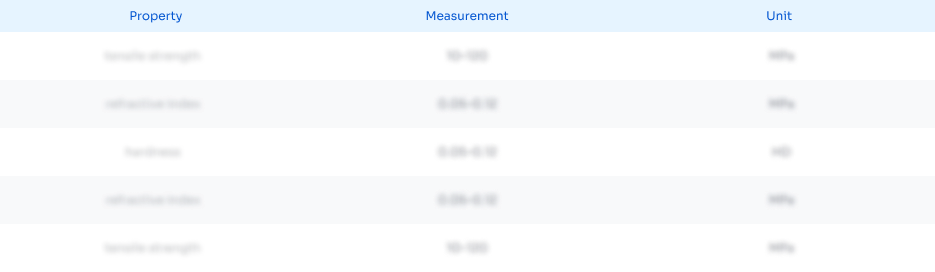
Abstract
Description
Claims
Application Information

- R&D
- Intellectual Property
- Life Sciences
- Materials
- Tech Scout
- Unparalleled Data Quality
- Higher Quality Content
- 60% Fewer Hallucinations
Browse by: Latest US Patents, China's latest patents, Technical Efficacy Thesaurus, Application Domain, Technology Topic, Popular Technical Reports.
© 2025 PatSnap. All rights reserved.Legal|Privacy policy|Modern Slavery Act Transparency Statement|Sitemap|About US| Contact US: help@patsnap.com