A backlight aluminum substrate pasting adhesive process
A technology of aluminum substrate and adhesive backing, which is applied in the field of lamp strip adhesive equipment, can solve the problems of fragile LED lamp beads and inability to operate with terminal substrates, and achieve the effect of preventing position shifting
- Summary
- Abstract
- Description
- Claims
- Application Information
AI Technical Summary
Problems solved by technology
Method used
Image
Examples
Embodiment 1
[0031] see Figure 1-3, in an embodiment of the present invention, a backlight aluminum substrate sticking glue process includes a workbench 1, a plurality of support columns 2 are fixedly connected to the bottom of the workbench 1, and a plurality of LEDs are provided on the top of the workbench 1 to avoid air slot 3, and the top of the workbench 1 is provided with a plurality of socket avoidance grooves 4, the middle end surface of the workbench 1 is socketed and connected with a C-shaped bracket 5, and one side of the plurality of support columns 2 is provided with a first chute 6, and The inside of the first chute 6 is socketed with a first slider 7, and the first slider 7 is fixedly connected with the C-shaped bracket 5, and the bottom end of the C-shaped bracket 5 is fixedly connected with two hydraulic rods 8, and the C-shaped bracket 5 The first bearing 9 is fitted and connected to both sides respectively, and the rotating end of the first bearing 9 is fixedly connecte...
Embodiment 2
[0033] see Figure 4 , the difference from Embodiment 1 is: the top of the workbench 1 is fixedly connected with a support frame 16, and the top of the support frame 16 is fitted with two guide tubes 17, and the two guide tubes 17 are internally threaded with a T-shaped bar 18 The bottom end of the T-bar 18 is fixedly connected with a third bearing 19, and the rotating end of the third bearing 19 is fixedly connected with a tank body 20, the inner wall of the tank body 20 is fixedly connected with a compression spring 21, and the bottom end of the compression spring 21 is fixedly connected with a C-shaped plate 22, the fourth bearing 23 is fixedly connected to both sides of the inner wall of the C-shaped plate 22, and the rotating end of the fourth bearing 23 is fixedly connected to a fitting roller 24, and the fitting roller 24 is parallel to the workbench 1, and The bonding roller 24 forms a rotating structure through the fourth bearing 23 and the C-shaped plate 22. The C-sh...
Embodiment 3
[0035] see figure 1 , Figure 5 The difference from Embodiment 1 is that: the top side of the workbench 1 is fixedly connected with a feeding bracket 25, and a feeding roller 26 is installed inside the feeding bracket 25, and the surface of the feeding roller 26 is movably sleeved with a back film The barrel 27, the middle end of the inner wall of the feeding bracket 25 is fixedly connected with a supporting plate 28, and the top of the supporting plate 28 is provided with a second chute 29, and the second chute 29 is socketed and inserted with two second sliders 30. The top of a second slider 30 is fixedly connected to the limiting plate 31, and the second slider 30 is internally threaded with a bolt 32, and the bolt 32 is movably connected to the second chute 29, and the second slider 30 is connected to the second slider 30 through the bolt 32. A fixable structure is formed between the chute 29, and the limiting plate 31 is flexibly connected with the adhesive reel 27, and ...
PUM
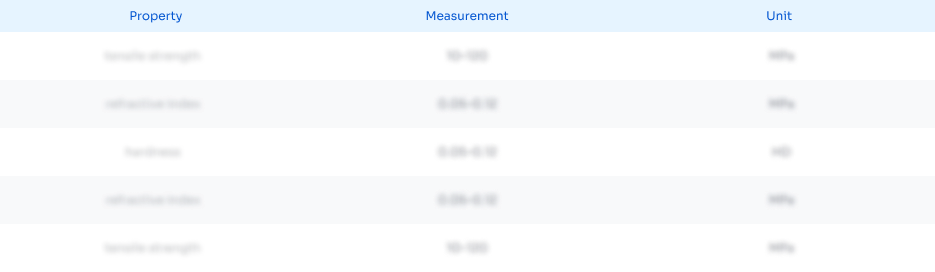
Abstract
Description
Claims
Application Information

- R&D Engineer
- R&D Manager
- IP Professional
- Industry Leading Data Capabilities
- Powerful AI technology
- Patent DNA Extraction
Browse by: Latest US Patents, China's latest patents, Technical Efficacy Thesaurus, Application Domain, Technology Topic, Popular Technical Reports.
© 2024 PatSnap. All rights reserved.Legal|Privacy policy|Modern Slavery Act Transparency Statement|Sitemap|About US| Contact US: help@patsnap.com