Omni-directional self-alignment mechanism for steel structure installation
An alignment mechanism and steel structure technology, applied in lifting devices, building construction, transportation and packaging, etc., can solve problems such as low efficiency, crane dumping, and high risk factor, so as to improve efficiency and reduce auxiliary adjustment time, the effect of reducing the suspension time
- Summary
- Abstract
- Description
- Claims
- Application Information
AI Technical Summary
Problems solved by technology
Method used
Image
Examples
Embodiment Construction
[0031] The following will clearly and completely describe the technical solutions in the embodiments of the present invention with reference to the accompanying drawings in the embodiments of the present invention. Obviously, the described embodiments are only some, not all, embodiments of the present invention.
[0032] refer to Figure 1-6 , an omnidirectional automatic alignment device for steel structure installation comprising;
[0033] The shell, the shell includes a shell, a bottom fixing plate 1 and an upper fixing plate 2, the bottom fixing plate 1 is fixedly installed on the bottom of the shell, and the upper fixing plate 2 is fixedly installed on the upper part of the shell;
[0034] Sensing device, the sensing component is installed on the steel member to sense the position deviation of the steel member;
[0035] Horizontal moving device, the horizontal moving device is installed on the bottom fixed plate 1, the horizontal moving device includes an adjustment asse...
PUM
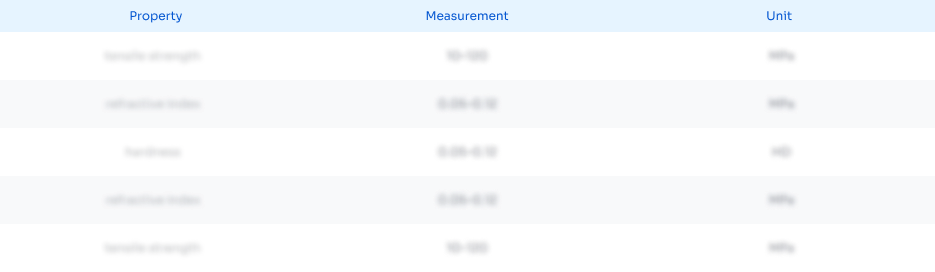
Abstract
Description
Claims
Application Information

- R&D
- Intellectual Property
- Life Sciences
- Materials
- Tech Scout
- Unparalleled Data Quality
- Higher Quality Content
- 60% Fewer Hallucinations
Browse by: Latest US Patents, China's latest patents, Technical Efficacy Thesaurus, Application Domain, Technology Topic, Popular Technical Reports.
© 2025 PatSnap. All rights reserved.Legal|Privacy policy|Modern Slavery Act Transparency Statement|Sitemap|About US| Contact US: help@patsnap.com