Robot frame structure
A frame structure and robot technology, applied in the substructure, vehicle parts, transportation and packaging, etc., can solve the problems of heavy weight, poor stiffness and shock absorption, and achieve high strength
- Summary
- Abstract
- Description
- Claims
- Application Information
AI Technical Summary
Problems solved by technology
Method used
Image
Examples
Embodiment Construction
[0029] A robot frame structure, see figure 1 with figure 2 , which includes a front frame 100, a rear frame 200, the front frame 100 is used for fixedly installing the front axle of the chassis and the middle seat, the battery controller, and the weight of the person; the rear frame 200 is used for fixedly installing the chassis rear axle and Support the weight of the item.
[0030] The front frame 100 is a double-layer beam structure formed by splicing several aluminum alloy profiles, which includes a first upper frame 120 and a first lower frame 130;
[0031] The rear frame 200 is a double-layer beam structure formed by splicing several aluminum alloy profiles, which includes a second upper frame 210 and a second lower frame 220;
[0032] The rear uprights arranged in parallel at the rear of the front frame 100 protrude from the first upper frame 120 , and the rear end faces of the rear longitudinal beams are fixedly connected to the cross beams and longitudinal beams at ...
PUM
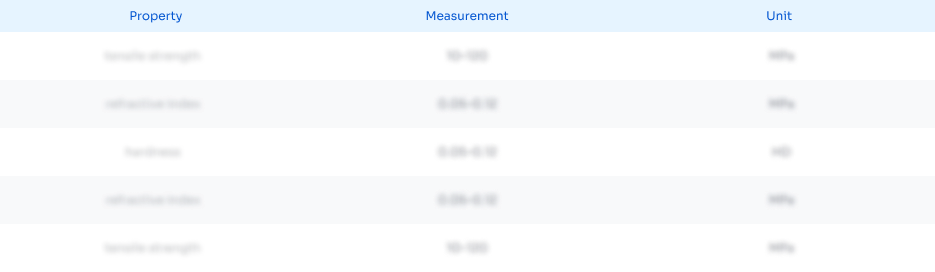
Abstract
Description
Claims
Application Information

- R&D Engineer
- R&D Manager
- IP Professional
- Industry Leading Data Capabilities
- Powerful AI technology
- Patent DNA Extraction
Browse by: Latest US Patents, China's latest patents, Technical Efficacy Thesaurus, Application Domain, Technology Topic, Popular Technical Reports.
© 2024 PatSnap. All rights reserved.Legal|Privacy policy|Modern Slavery Act Transparency Statement|Sitemap|About US| Contact US: help@patsnap.com