Variable line girder numerical control driving system and working process thereof
A drive system and girder technology, applied to monorail systems, elevated railway systems with suspended vehicles, motor vehicles, etc., can solve problems such as the inability to ensure the accurate docking of switch rails and fixed rails, and achieve high reliability and improved Operational accuracy and improved reliability
- Summary
- Abstract
- Description
- Claims
- Application Information
AI Technical Summary
Problems solved by technology
Method used
Image
Examples
Embodiment 1
[0073] like Figure 1-2 shown in figure 1 In the structural schematic diagram of the suspended freight monorail three-opening turnout, the fixed monorail open box track beam a is two I-shaped beams ( Figure 1-2 Simplified in , the same below), the line-changing monorail open box track beam c is also two I-shaped beams arranged in parallel in space; the three-track open box track beam e is composed of six mutually fixed The two I-shaped girders in the center of the three-track open box track beam e are arranged in parallel in space; the two I-shaped girders on both sides are respectively arranged in parallel in space; the central I-shaped girder and the two sides The included angle between the I-shaped girders is just equal to the line change angle of the turnout. The two change-line rails f are respectively placed on the upper surface of the lower floor inside the I-shaped girder (inside the vertical plate of the I-shaped girder) of the fixed monorail open box track beam a ...
Embodiment 2
[0090] On the basis of Embodiment 1, the present invention also provides a working process of a line-changing girder numerical control drive system, including a debugging process and a working process.
[0091] 1. Debugging process
[0092] 1) Left working point setting
[0093] attached Figure 1 to Figure 11 As shown, the open box-shaped track beam 006 of the line-changing monorail is in the neutral position. Firstly, the two servo motors 125 are started at the same speed in the jogging mode, and the two driving wheels B127 are driven to rotate through the two reducers 124 and the two rotating shafts B129. , the two traveling wheels A121 also rotate at the same speed; thereby driving the line-changing monorail open box-type track beam 006 to turn counterclockwise through a three-way turnout angle, and observe the mutual position of the line-changing track f and the three-way switch rail d In this situation, the two servo motors 125 are repeatedly jogged in forward and reve...
PUM
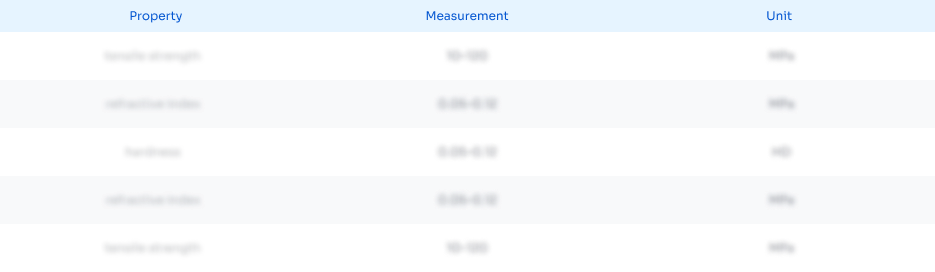
Abstract
Description
Claims
Application Information

- R&D
- Intellectual Property
- Life Sciences
- Materials
- Tech Scout
- Unparalleled Data Quality
- Higher Quality Content
- 60% Fewer Hallucinations
Browse by: Latest US Patents, China's latest patents, Technical Efficacy Thesaurus, Application Domain, Technology Topic, Popular Technical Reports.
© 2025 PatSnap. All rights reserved.Legal|Privacy policy|Modern Slavery Act Transparency Statement|Sitemap|About US| Contact US: help@patsnap.com