A kind of high strength and high thermal conductivity nylon composite material and preparation method thereof
A nylon composite material, high thermal conductivity technology, applied in the field of high strength and high thermal conductivity nylon composite material and its preparation, can solve the problems of graphene and carbon nanotubes with small particle size, difficult to achieve dispersion and easy agglomeration by melt blending, and achieve interface Strong interaction force, improving mechanical properties and thermal stability, and reducing the effect of interface thermal resistance
- Summary
- Abstract
- Description
- Claims
- Application Information
AI Technical Summary
Problems solved by technology
Method used
Image
Examples
Embodiment 1
[0047] 1.5kg nylon 66, 450g spherical alumina, 7.5g silicone powder, 3g antioxidant 1098, 3g antioxidant 626 were vacuum-dried at 85°C for 12h, extruded through twin-screw granules, and then injection-molded into mechanical splines and discs.
[0048] The temperature of each zone of the extruder: Zone 1: 260℃, Zone 2: 265℃, Zone 3: 270℃, Zone 4: 275℃, Zone 5: 280℃, Zone 6: 280℃, Zone 7: 275℃, Zone 8 : 270℃, Zone 9: 270℃, Zone 10: 275℃. The specific performance is shown in Table 2.
Embodiment 2
[0050] 1.35kg nylon 66, 150g graphene nylon 6 masterbatch, 450g spherical alumina, 7.5g silicone powder, 3g antioxidant 1098, 3g antioxidant 626 were vacuum-dried at 85°C for 12h, and manufactured by twin-screw extrusion. pellets, and then injection-molded mechanical splines and discs.
[0051] The temperature of each zone of the extruder: Zone 1: 260℃, Zone 2: 265℃, Zone 3: 270℃, Zone 4: 275℃, Zone 5: 280℃, Zone 6: 280℃, Zone 7: 275℃, Zone 8 : 270℃, Zone 9: 270℃, Zone 10: 275℃. The specific performance is shown in Table 2.
Embodiment 3
[0053] 1.35kg nylon 66, 150g graphene nylon 6 masterbatch, 450g spherical alumina, 150g carbon fiber, 7.5g silicone powder, 3g antioxidant 1098, 3g antioxidant 626 were vacuum-dried at 85°C for 12h, and passed through twin screw Extrusion granulation, then injection molding mechanical splines and discs.
[0054] The temperature of each zone of the extruder: Zone 1: 260℃, Zone 2: 265℃, Zone 3: 270℃, Zone 4: 275℃, Zone 5: 280℃, Zone 6: 280℃, Zone 7: 275℃, Zone 8 : 270℃, Zone 9: 270℃, Zone 10: 275℃. The specific performance is shown in Table 2.
PUM
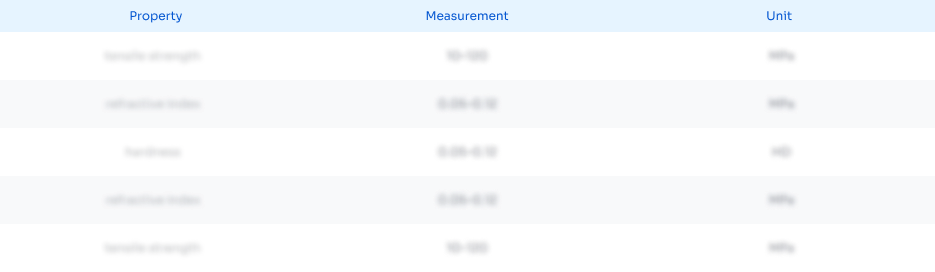
Abstract
Description
Claims
Application Information

- Generate Ideas
- Intellectual Property
- Life Sciences
- Materials
- Tech Scout
- Unparalleled Data Quality
- Higher Quality Content
- 60% Fewer Hallucinations
Browse by: Latest US Patents, China's latest patents, Technical Efficacy Thesaurus, Application Domain, Technology Topic, Popular Technical Reports.
© 2025 PatSnap. All rights reserved.Legal|Privacy policy|Modern Slavery Act Transparency Statement|Sitemap|About US| Contact US: help@patsnap.com