Shaftless electric engine for aircraft, control method and aircraft
An electric engine and aircraft technology, which is used in aircraft parts, aircraft power transmission, aircraft power units, etc., can solve problems such as narrow use range, limit efficiency, sound pollution, etc., to avoid speed limit and power output limit, The effect of high energy use efficiency and avoidance of noise pollution
- Summary
- Abstract
- Description
- Claims
- Application Information
AI Technical Summary
Problems solved by technology
Method used
Image
Examples
Embodiment 1
[0040] Such as Figures 1 to 10 As shown, the shaftless electric motor used for aircraft includes an engine casing 1, the front end of the engine casing 1 has an air inlet 2, and the rear end has a tail nozzle 3, and the distance between the air inlet 2 and the tail nozzle 3 is from front to back. The first group of magnetic levitation rotating mechanisms, the second group of magnetic levitation rotating mechanisms, and the third group of magnetic levitation rotating mechanisms are installed in sequence, and the combustion chamber 4 is between the second group of magnetic levitation rotating mechanisms and the third group of magnetic levitation rotating mechanisms;
[0041] The magnetic levitation rotating mechanism includes a casing 14, which is fixedly connected with the engine casing 1. There is an installation cavity in the casing 14 to provide an installation area for the stator. Stator, the stator is made of silicon steel material with good magnetic permeability, the sta...
Embodiment 2
[0057] Such as Figure 11 As shown, on the basis of Embodiment 1, each set of magnetic levitation rotating mechanism includes at least two stages of stators and blades 22 connected in series, that is, the fans of the magnetic levitation, the compressors of the magnetic levitation, and the turbogenerators of the magnetic levitation can be arranged as two or more stages in series. The structure of the stator and the blades 22, in this embodiment, is specifically set as a three-stage series structure to increase the output power.
[0058] An aircraft, the aircraft (not shown in the figure) is equipped with the shaftless electric motor described in Embodiment 1 or Embodiment 2.
PUM
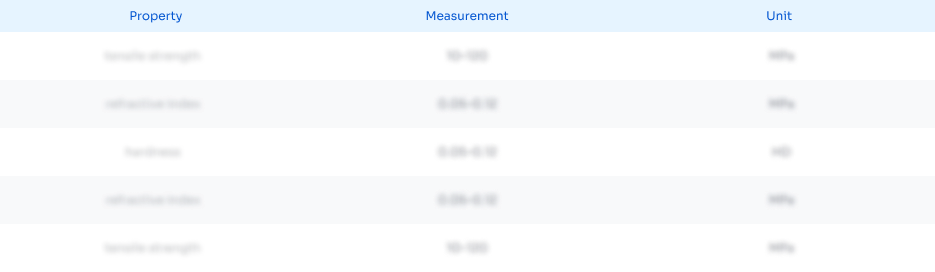
Abstract
Description
Claims
Application Information

- R&D
- Intellectual Property
- Life Sciences
- Materials
- Tech Scout
- Unparalleled Data Quality
- Higher Quality Content
- 60% Fewer Hallucinations
Browse by: Latest US Patents, China's latest patents, Technical Efficacy Thesaurus, Application Domain, Technology Topic, Popular Technical Reports.
© 2025 PatSnap. All rights reserved.Legal|Privacy policy|Modern Slavery Act Transparency Statement|Sitemap|About US| Contact US: help@patsnap.com