Machining method for air inlet fairing of air compressor of heavy-duty gas turbine
A technology of air intake fairing and processing method, which is applied to the processing of fairings and the processing of air intake fairings of heavy-duty gas turbine compressors, and can solve the problem of no clamping position and the like
- Summary
- Abstract
- Description
- Claims
- Application Information
AI Technical Summary
Problems solved by technology
Method used
Image
Examples
specific Embodiment approach 1
[0026] Specific implementation mode one: combine Figure 1 to Figure 6 Illustrate this embodiment, a kind of auxiliary fixture that is used for processing the intake fairing of heavy-duty gas turbine compressor described in this embodiment, this processing method is carried out according to the following steps:
[0027] Step 1: Since the inner hole of the workpiece 1 is a casting surface, no processing is required. In order to find out the uniform wall thickness, the concentricity between the outer circle of the casting blank and the inner hole is re-measured by scribing; At the outer blank margin of the end clamping position, the alignment datum plane and outer circular molding line are used for the turning process;
[0028] Step 2: leave margins at the positions of the plurality of flange holes 1-2, drill six process screw holes evenly distributed on the outer surface of the workpiece 1 along the circumferential direction, and the six process screw holes are used to connect ...
specific Embodiment approach 2
[0033] Specific implementation mode two: combination Figure 3-Figure 6 To describe this embodiment, the number of flange holes 1-2 in this embodiment is eighteen, and the eighteen flange holes 1-2 are evenly distributed along the circumferential direction.
[0034] Other components and connections are the same as those in the first embodiment.
specific Embodiment approach 3
[0035] Specific implementation mode three: combination Figure 3 to Figure 6 To describe this embodiment, the flange hole 1-2 in this embodiment is a stepped hole.
[0036] Other compositions and connections are the same as those in Embodiment 1 or 2.
PUM
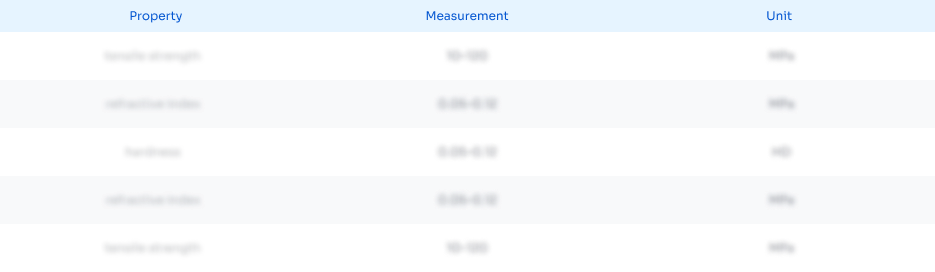
Abstract
Description
Claims
Application Information

- R&D
- Intellectual Property
- Life Sciences
- Materials
- Tech Scout
- Unparalleled Data Quality
- Higher Quality Content
- 60% Fewer Hallucinations
Browse by: Latest US Patents, China's latest patents, Technical Efficacy Thesaurus, Application Domain, Technology Topic, Popular Technical Reports.
© 2025 PatSnap. All rights reserved.Legal|Privacy policy|Modern Slavery Act Transparency Statement|Sitemap|About US| Contact US: help@patsnap.com