Large sleeve forming die and combined extrusion forming process thereof
A technology for forming molds and sleeves, which is applied in the direction of manufacturing tools, metal processing equipment, forging/pressing/hammer devices, etc., and can solve problems such as unfavorable use, waste, and poor utilization of materials
- Summary
- Abstract
- Description
- Claims
- Application Information
AI Technical Summary
Problems solved by technology
Method used
Image
Examples
Embodiment Construction
[0029] In order to make the technical means, creative features, goals and effects achieved by the present invention easy to understand, the present invention will be further described below in conjunction with specific embodiments.
[0030] like Figure 1-7 As shown, a large-scale sleeve molding die comprises a lower mold body 1, a lower mold base 11, and an upper mold body 3. The upper end of the upper mold body 3 is fixedly connected with an upper mold connecting seat 8, and the upper end of the upper mold connecting seat 8 is fixed. Connected with the upper template 2, the inner wall of the upper mold body 3 is provided with an upper punch 9, the inner wall of the lower mold body 1 is provided with a mold cavity 6, the bottom of the mold cavity 6 is positioned and connected with a positioning cylinder 12, and the upper end of the positioning cylinder 12 is positioned and connected There is a lower punch 10, the lower end of the lower mold base 11 is provided with a position...
PUM
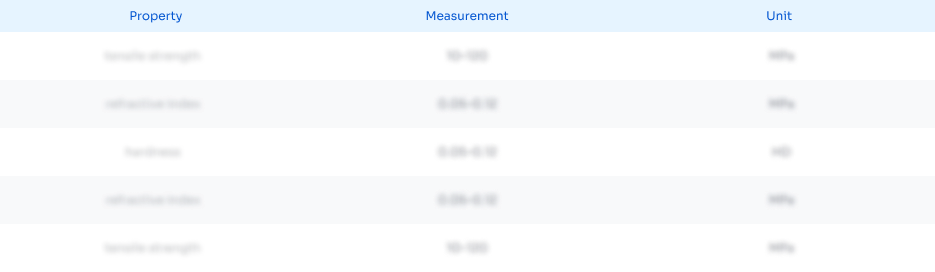
Abstract
Description
Claims
Application Information

- R&D Engineer
- R&D Manager
- IP Professional
- Industry Leading Data Capabilities
- Powerful AI technology
- Patent DNA Extraction
Browse by: Latest US Patents, China's latest patents, Technical Efficacy Thesaurus, Application Domain, Technology Topic, Popular Technical Reports.
© 2024 PatSnap. All rights reserved.Legal|Privacy policy|Modern Slavery Act Transparency Statement|Sitemap|About US| Contact US: help@patsnap.com