Cylindrical surface element error model under multi-tolerance coupling effect and solving method
An error model and cylindrical surface technology, which is applied in the field of establishment and solution of cylindrical surface element error models under the action of multi-tolerance coupling, can solve problems such as uncertain error ranges, achieve the effect of verifying correctness and avoiding waste of manufacturing costs
- Summary
- Abstract
- Description
- Claims
- Application Information
AI Technical Summary
Problems solved by technology
Method used
Image
Examples
Embodiment Construction
[0040] The technical scheme of the present invention is further described below
[0041] see Figure 1-Figure 4 , the specific steps of the establishment and solution method of the error model of the cylindrical surface element under the multi-tolerance coupling effect of the present invention are as follows
[0042] Step 1: Combining the SDT small displacement screw method with the part tolerance, using the small changes of six degrees of freedom to describe the error of the geometric elements of the part. In SDT, V=(μ, ν, ω, α, β, γ), where φ=(μ, ν, ω) represents the small change vector of three degrees of freedom translation along the coordinate system x, y, z, d=(α, β, γ) represents a small change vector rotating along the three degrees of freedom of the coordinate system x, y, z. For different constraints, some parameters in different types of tolerance SDT expressions are zero, that is, when a geometric element rotates or translates along a certain coordinate axis, its...
PUM
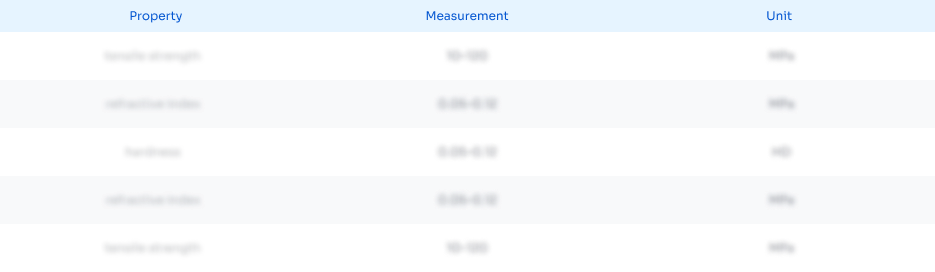
Abstract
Description
Claims
Application Information

- R&D Engineer
- R&D Manager
- IP Professional
- Industry Leading Data Capabilities
- Powerful AI technology
- Patent DNA Extraction
Browse by: Latest US Patents, China's latest patents, Technical Efficacy Thesaurus, Application Domain, Technology Topic, Popular Technical Reports.
© 2024 PatSnap. All rights reserved.Legal|Privacy policy|Modern Slavery Act Transparency Statement|Sitemap|About US| Contact US: help@patsnap.com