Arm support fatigue analysis method
A fatigue analysis and boom technology, applied in the field of stress analysis, can solve problems such as spending a lot of time in inspection and proofreading, regional and size deviation, and difficulty in obtaining, so as to improve the accuracy of fatigue analysis, reduce the difficulty of calculation, and simplify the calculation process. Effect
- Summary
- Abstract
- Description
- Claims
- Application Information
AI Technical Summary
Problems solved by technology
Method used
Image
Examples
Embodiment Construction
[0026] The present invention will be further described below in conjunction with the examples and drawings, but the embodiments of the present invention are not limited thereto.
[0027] see figure 1 , the boom fatigue analysis method of the present embodiment includes the following steps:
[0028] (1) Establish a three-dimensional model according to the actual shape and size of the boom, establish a network model of the boom through the finite element method, and set the parameters of the boom. The boom parameters include material properties, density, and modulus of elasticity. Specifically, yield stress, minimum tensile strength, Poisson's ratio, etc. are also included.
[0029] (2) Use simulation software to simulate the motion of the boom under normal working conditions, and measure the motion data of the boom that changes with time in a cycle movement. The motion data includes the load size and position; through the motion data of the boom Carry out discretization to f...
PUM
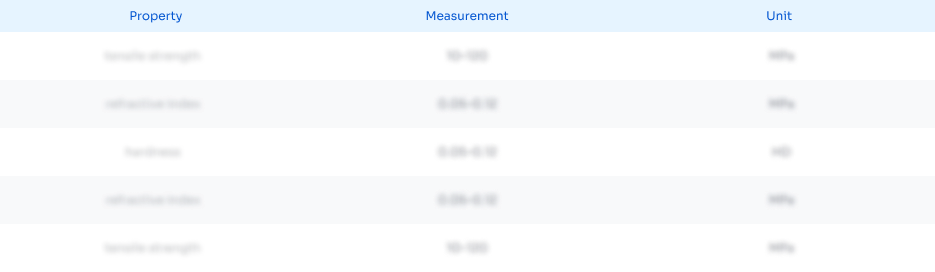
Abstract
Description
Claims
Application Information

- R&D
- Intellectual Property
- Life Sciences
- Materials
- Tech Scout
- Unparalleled Data Quality
- Higher Quality Content
- 60% Fewer Hallucinations
Browse by: Latest US Patents, China's latest patents, Technical Efficacy Thesaurus, Application Domain, Technology Topic, Popular Technical Reports.
© 2025 PatSnap. All rights reserved.Legal|Privacy policy|Modern Slavery Act Transparency Statement|Sitemap|About US| Contact US: help@patsnap.com