Novel permanent magnet synchronous motor position observation method with dynamic error compensation function
A permanent magnet synchronous motor, dynamic error technology, applied in the direction of motor generator control, generator control, motor control, etc., can solve the problems of increasing the complexity of the drive system, reducing the reliability of the system, increasing the cost, etc. The effect of perceived performance
- Summary
- Abstract
- Description
- Claims
- Application Information
AI Technical Summary
Problems solved by technology
Method used
Image
Examples
Embodiment 1
[0049] see Figure 1-2 , a novel position observation method for permanent magnet synchronous motors with dynamic error compensation, including the following steps:
[0050] S1. In the α-β static reference frame, based on the equivalent EMF model, the stator voltage and current model of the embedded permanent magnet synchronous motor (IPMSM) is established, specifically:
[0051]
[0052] In the formula, are the equivalent EMFs, u α , u β is the stator voltage; i α , i β is the stator current in the α-β stationary reference frame; R s is the stator resistance; L q is the q-axis inductance;
[0053] S2. Neglecting the dynamic characteristics of the d-axis stator current, then Thus the formula (1) mentioned in S1 can be simplified as
[0054]
[0055] According to formula (2), the α and β components of the equivalent EMF model are respectively the rotor position θ r ' of the sine and cosine functions, where θ' r can be obtained from the tangent function tan -...
PUM
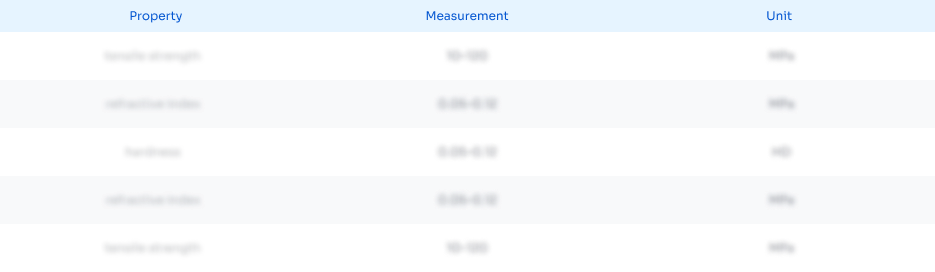
Abstract
Description
Claims
Application Information

- R&D Engineer
- R&D Manager
- IP Professional
- Industry Leading Data Capabilities
- Powerful AI technology
- Patent DNA Extraction
Browse by: Latest US Patents, China's latest patents, Technical Efficacy Thesaurus, Application Domain, Technology Topic, Popular Technical Reports.
© 2024 PatSnap. All rights reserved.Legal|Privacy policy|Modern Slavery Act Transparency Statement|Sitemap|About US| Contact US: help@patsnap.com