Warpage deformation prediction method for thin-walled components in space envelope forming
A technology of thin-walled components and prediction methods, applied in the direction of instrument, geometric CAD, design optimization/simulation, etc., can solve the problems of component folding, rupture and scrap, warping deformation, small thickness of thin-walled components, etc., to shorten the product development cycle, The effect of improving design efficiency and improving accuracy
- Summary
- Abstract
- Description
- Claims
- Application Information
AI Technical Summary
Problems solved by technology
Method used
Image
Examples
Embodiment Construction
[0056] In order to have a clearer understanding of the technical features, purposes and effects of the present invention, the specific implementation manners of the present invention will now be described in detail with reference to the accompanying drawings.
[0057] A method for predicting warping deformation of a thin-walled component space envelope forming according to the present invention comprises the following steps:
[0058] S1. Determine the principle of space envelope forming of thin-walled components. The initial state of space envelope forming of thin-walled members is as follows: figure 1 as shown, figure 1Among them, 1 is the enveloping mold, 2 is the blank, and 3 is the lower mold. The envelope mold rotates around its own axis and the central axis of the thin-walled member at a speed of n=4rad / s, and the lower mold drives the blank placed in the lower mold to approach the envelope mold at a feed speed of v=2mm / s. With the increase of the feed rate of the low...
PUM
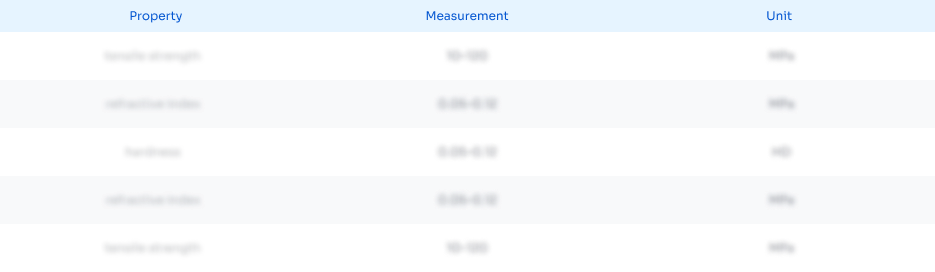
Abstract
Description
Claims
Application Information

- Generate Ideas
- Intellectual Property
- Life Sciences
- Materials
- Tech Scout
- Unparalleled Data Quality
- Higher Quality Content
- 60% Fewer Hallucinations
Browse by: Latest US Patents, China's latest patents, Technical Efficacy Thesaurus, Application Domain, Technology Topic, Popular Technical Reports.
© 2025 PatSnap. All rights reserved.Legal|Privacy policy|Modern Slavery Act Transparency Statement|Sitemap|About US| Contact US: help@patsnap.com