Piezoelectric Energy Harvesting Experimental Device for Flow-Induced Vibration of Film Wing
A test device and vibration pressure technology, which is applied in the direction of measuring devices, aerodynamic tests, and testing electrical devices in transportation, etc., can solve the problem of affecting the aerodynamic performance of film wings, the passive deformation of structures becomes smaller, and the fatigue fracture of piezoelectric sheets, etc. problems, to achieve the effect of improving energy collection efficiency, not easy to fatigue and fracture, and long service life
- Summary
- Abstract
- Description
- Claims
- Application Information
AI Technical Summary
Problems solved by technology
Method used
Image
Examples
Embodiment Construction
[0029] The present invention will be further described in detail with reference to the accompanying drawings and embodiments.
[0030] The piezoelectric energy harvesting test device for flow-induced vibration of a thin film wing of the present invention comprises a support 1, a wing connecting turntable 2, a thin film wing 3 and a piezoelectric sheet 4, such as figure 1 shown.
[0031] The support 1 is used to support the membrane wing 3, and has left and right baffles 101, two bottom beams 102 and a dial 103 installed on the left and right baffles 101 along the left and right directions. Among them, the left and right baffles 101 are rectangular plates with round holes in the center, perpendicular to the two bottom beams 102 , arranged near the two ends of the two bottom beams 102 , and the bottom edges are fixed to the two bottom beams 102 . The film wings 3 are arranged between the inner surfaces of the left and right baffles 101 . The dial 103 is a disc, which is fixed ...
PUM
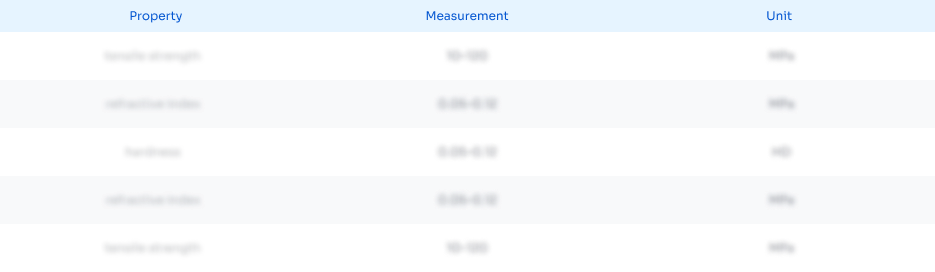
Abstract
Description
Claims
Application Information

- R&D
- Intellectual Property
- Life Sciences
- Materials
- Tech Scout
- Unparalleled Data Quality
- Higher Quality Content
- 60% Fewer Hallucinations
Browse by: Latest US Patents, China's latest patents, Technical Efficacy Thesaurus, Application Domain, Technology Topic, Popular Technical Reports.
© 2025 PatSnap. All rights reserved.Legal|Privacy policy|Modern Slavery Act Transparency Statement|Sitemap|About US| Contact US: help@patsnap.com