Systematic template for high-speed rail base adopting glass fiber panel
A track base and formwork technology, which is applied to tracks, track laying, track maintenance, etc., can solve the problems of easy corrosion on the surface of steel formwork, increased maintenance costs in the later period, and large weight of the formwork itself. Good molding effect
- Summary
- Abstract
- Description
- Claims
- Application Information
AI Technical Summary
Problems solved by technology
Method used
Image
Examples
Embodiment Construction
[0022] In order to further illustrate the present invention, the invention will be described in detail below in conjunction with the accompanying drawings and embodiments, but they should not be construed as limiting the protection scope of the present invention.
[0023] Such as figure 1 As shown, the present invention adopts a systemized formwork for a high-speed rail track base using a glass fiber panel, including a formwork side form 1, a fixing device frame 2, a blocking plate 3, a load beam 4, a groove formwork 5 and a T-bolt 6; The formwork side form 1 and the blocking plate 3 are each two pieces, the formwork side form 1 and the blocking plate 3 form a rectangle, the groove formwork 5 is a rectangle, and is arranged at the center of the rectangle, and the groove formwork 5 is vertical Four T-shaped bolts 6 are connected; the formwork side form 1 is connected with the fixture frame 2, and the formwork side form 1 is vertically fixed on the ground through the fixture fra...
PUM
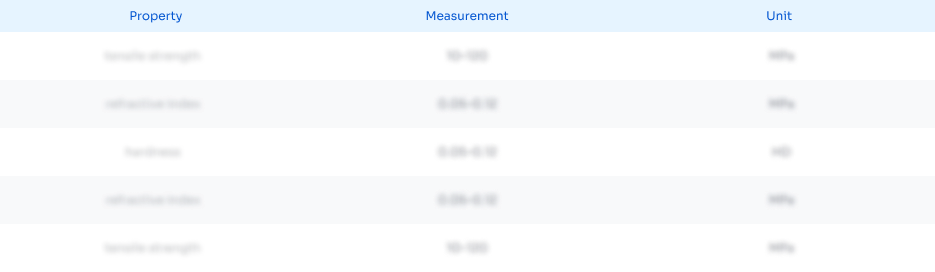
Abstract
Description
Claims
Application Information

- R&D
- Intellectual Property
- Life Sciences
- Materials
- Tech Scout
- Unparalleled Data Quality
- Higher Quality Content
- 60% Fewer Hallucinations
Browse by: Latest US Patents, China's latest patents, Technical Efficacy Thesaurus, Application Domain, Technology Topic, Popular Technical Reports.
© 2025 PatSnap. All rights reserved.Legal|Privacy policy|Modern Slavery Act Transparency Statement|Sitemap|About US| Contact US: help@patsnap.com