Textile fabric coating equipment
A technology for textile fabrics and coatings, applied in the field of textile fabrics, can solve the problems of color confusion on the upper surface of textile fabrics and increase in reject rate, and achieve the effect of avoiding color confusion and reducing reject rate.
- Summary
- Abstract
- Description
- Claims
- Application Information
AI Technical Summary
Problems solved by technology
Method used
Image
Examples
Embodiment 1
[0026] see Figure 1-Figure 5 , the specific embodiment of the present invention is as follows: a kind of textile fabric coating equipment, its structure comprises base 1, coating machine 2, feeding belt 3, console 4, power machine 5, described base 1 top surface and coating machine 2 bottom surfaces Welding connection, the back of the console 4 is embedded in the front of the coating machine 2, the right side of the feeding belt 3 is nested and connected to the left side of the power machine 5, and the front side of the power machine 5 is welded to the back of the coating machine 2; The layer machine 2 includes a shell 21, a hot air machine 22, an air extraction pipe 23, a paint box 24, and a smearing rod 25. The inside of the shell 21 is welded to the outer layer of the air heat machine 22, and the bottom of the air extraction pipe 23 is embedded in the heat air machine 22. The right side of the paint box 24 and the left side of the smear rod 25 are connected to each other a...
Embodiment 2
[0032] see Figure 6-Figure 8The specific embodiments of the present invention are as follows: the air guide plate A25 includes a plate body B1, a chuck B2, a backflow tank B3, and a blocking bar B4, the top surface of the board body B1 is embedded and connected to the bottom surface of the chuck B2, and the backflow The groove B3 and the left side of the plate body B1 are integrally formed, and the bottom of the blocking bar B4 is engaged with the inner layer of the backflow groove B3. There are multiple backflow grooves B3, and the gaps between the multiple backflow grooves B3 are evenly distributed on the plate. The left side of body B1 is conducive to increasing the number of backflows and making the filtering effect better.
[0033] Wherein, the blocking bar B4 includes a card wheel B41, a connecting bar B42, a bearing bar B43, a contact groove B44, and a sticky head B45. B44 and the outer layer of the bearing rod B43 are integrally formed, the bottom of the sticky head ...
PUM
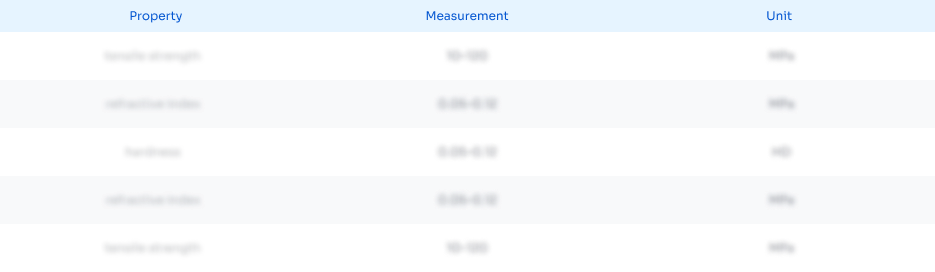
Abstract
Description
Claims
Application Information

- Generate Ideas
- Intellectual Property
- Life Sciences
- Materials
- Tech Scout
- Unparalleled Data Quality
- Higher Quality Content
- 60% Fewer Hallucinations
Browse by: Latest US Patents, China's latest patents, Technical Efficacy Thesaurus, Application Domain, Technology Topic, Popular Technical Reports.
© 2025 PatSnap. All rights reserved.Legal|Privacy policy|Modern Slavery Act Transparency Statement|Sitemap|About US| Contact US: help@patsnap.com