Turnover type hot galvanizing pretreatment production system and method
A production system and production method technology, applied in hot-dip plating process, metal material coating process, coating, etc., can solve problems such as low safety performance, inability to achieve energy saving and environmental protection, and poor degreasing effect
- Summary
- Abstract
- Description
- Claims
- Application Information
AI Technical Summary
Problems solved by technology
Method used
Image
Examples
Embodiment Construction
[0050] In order to enable those skilled in the art to better understand the solutions of the present invention, the technical solutions in the embodiments of the invention will be clearly and completely described below in conjunction with the drawings in the embodiments of the present invention. Obviously, the described embodiments are only It is a part of embodiments of the present invention, but not all embodiments. Based on the embodiments of the present invention, all other embodiments obtained by persons of ordinary skill in the art without making creative efforts shall fall within the protection scope of the present invention.
[0051] Such as Figure 1-20 As shown, a flip-type hot-dip galvanizing pretreatment production system includes a frame 1, a plurality of tanks 2 arranged in the frame 1 along the length direction of the frame 1, and correspondingly arranged in each tank The overturning mechanism 3 in 2, a plurality of tanks 2 are independent of each other, and ea...
PUM
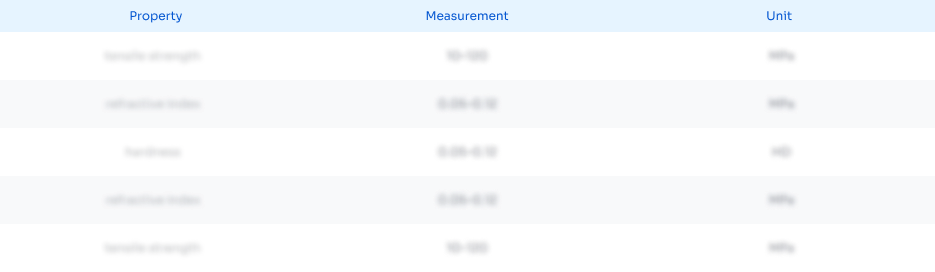
Abstract
Description
Claims
Application Information

- R&D Engineer
- R&D Manager
- IP Professional
- Industry Leading Data Capabilities
- Powerful AI technology
- Patent DNA Extraction
Browse by: Latest US Patents, China's latest patents, Technical Efficacy Thesaurus, Application Domain, Technology Topic, Popular Technical Reports.
© 2024 PatSnap. All rights reserved.Legal|Privacy policy|Modern Slavery Act Transparency Statement|Sitemap|About US| Contact US: help@patsnap.com