Mechanical arm with high precision and control method thereof
A manipulator and precision technology, applied in the field of manipulators, which can solve the problems of labor-intensive and unstable manipulators
- Summary
- Abstract
- Description
- Claims
- Application Information
AI Technical Summary
Problems solved by technology
Method used
Image
Examples
Embodiment 1
[0042] A high-precision manipulator, such as Figure 1-4 As shown, including the body 1, the bottom outer wall of the body 1 is fixed with four legs 2 by bolts; the top outer wall of the body 1 is provided with three placement grooves 37, and the inner walls of the three placement grooves 37 are all fixed by bolts. Hydraulic cylinder 18, the extension ends of the three hydraulic cylinders 18 are all fixed with the lower connecting seat 3 by bolts, the three lower connecting seats 3 form sliding fit with the three placement grooves 37 respectively, the lower connecting seat 3 is a C-shaped structure, three One side of the inner wall of the lower connecting seat 3 is slidably connected with an electric telescopic assembly 10 through a slider, one side of the outer wall of the three electric telescopic assemblies 10 is connected with an upper connecting seat 16 through a rotating shaft, and the top outer walls of the three upper connecting seats 16 are The same fixed seat 5 is fi...
Embodiment 2
[0049] A method of controlling a manipulator with high precision, such as Figure 1-7 shown, including the following steps:
[0050] S1: Load the objects to be transported into the collection box 12;
[0051] S2: Control and start two first motors 7 that rotate asynchronously, and drive the moving rod 8 to move forward and backward through the gear 19;
[0052] S3: When the infrared receiver 6 receives the light curtain signal from the infrared emitter 9, it controls the first motor 7 to turn off, and then adjusts the lifting structure to drive the manipulator 4 to descend to pick up the object;
[0053] S4: when picking and transferring objects, the infrared light 34 is turned on, and its light is used as a reference point for the manipulator 4 to pick;
[0054] S5: The camera 31 captures the image in real time and transmits it to the display screen 11 for display as a reference;
[0055] S6: After retrieving the material successfully, control and start the first motor 7 t...
PUM
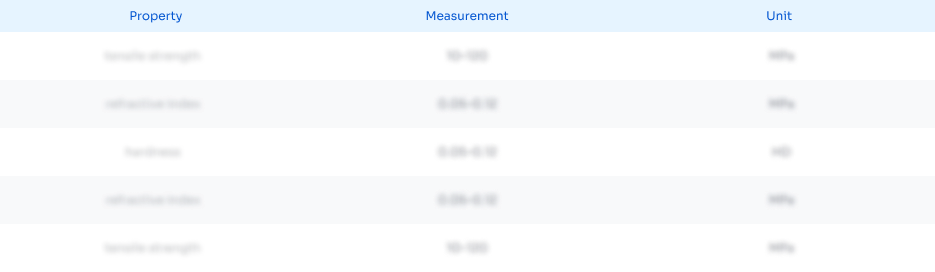
Abstract
Description
Claims
Application Information

- R&D
- Intellectual Property
- Life Sciences
- Materials
- Tech Scout
- Unparalleled Data Quality
- Higher Quality Content
- 60% Fewer Hallucinations
Browse by: Latest US Patents, China's latest patents, Technical Efficacy Thesaurus, Application Domain, Technology Topic, Popular Technical Reports.
© 2025 PatSnap. All rights reserved.Legal|Privacy policy|Modern Slavery Act Transparency Statement|Sitemap|About US| Contact US: help@patsnap.com