A stacker pick-and-place cargo system and its application method
A stacker and cargo technology, applied in the field of logistics and warehousing automation, can solve the problems of reduced system stability, inapplicability, and increased program logic complexity, and achieve the effects of improved operational stability, consistent program interface, and improved accuracy
- Summary
- Abstract
- Description
- Claims
- Application Information
AI Technical Summary
Problems solved by technology
Method used
Image
Examples
Embodiment 1
[0042] Example 1 Exclusion of Abnormal Goods
[0043] The cargo initial data information W0*H0*D0 is 1000mm*1200mm*1000mm, and the cargo platform frame threshold is 1200mm*1300mm*1200mm;
[0044] Step 1: PC task scheduling;
[0045] The upper computer enters the initial data information W0*H0*D0 of the goods as 1000mm*1200mm*1000mm, and sends the task to the stacker to perform the goods warehousing task;
[0046] Step 2: Cargo shape data scanning and cargo shape out-of-limit detection when the goods enter the loading platform;
[0047] The left vision camera 1 scans the goods on the right side of the loading platform or the right vision camera 2 scans the goods on the left side of the loading platform to obtain the actual dimensions of the goods. Width W1=1002mm and height H1=1332mm, analyze and judge The relationship between width W1=1002mm and height H1=1332mm and the permissible threshold of the cargo platform frame is 1200mm*1300mm*1200mm. It is obtained that the cargo h...
Embodiment 2
[0048] Embodiment 2 The absolute value of the difference between the actual external dimensions of the goods and the initial data exceeds the error range m, and they are placed on the retractable shelf as abnormal goods
[0049] The cargo initial data information W0*H0*D0 is 1000mm*1200mm*1000mm, the cargo platform frame threshold is 1200mm*1300mm*1200mm, m=50mm;
[0050] Step 1: PC task scheduling;
[0051] The upper computer enters the cargo information W0*H0*D0 as 1000mm*1200mm*1000mm, and sends the task to the stacker to perform the cargo warehousing task;
[0052] Step 2: Cargo shape data scanning and cargo shape out-of-limit detection when the goods enter the loading platform;
[0053] The left vision camera 1 scans the goods on the right side of the loading platform or the right vision camera 2 scans the goods on the left side of the loading platform to obtain the actual dimensions of the goods. Width W=1002mm and height H=1120mm, analyze and judge The relationship be...
Embodiment 3
[0057] Example 3: Put the goods into the target location
[0058] The initial cargo data information W0*H0*D0 is 1000mm*1200mm*1000mm, the cargo platform frame threshold is 1200mm*1300mm*1200mm, m=50mm, n is greater than 0;
[0059] Step 1: PC task scheduling;
[0060] The upper computer enters the cargo information W0*H0*D0 as 1000mm*1200mm*1000mm, and the stacker performs the cargo warehousing task;
[0061] Step 2: Cargo shape data scanning and cargo shape out-of-limit detection when the goods enter the loading platform;
[0062] The left vision camera 1 scans the goods on the right side of the cargo platform or the right vision camera 2 scans the goods on the left side of the cargo platform to obtain the actual dimensions of the goods. Width W1=1002mm and height H1=1220mm, analyze and judge Width W1=1002mm, height H1=1220mm and the allowable threshold of the cargo platform frame 1200mm*1300mm*1200mm, it is concluded that the width W1 or height H1 does not exceed the thre...
PUM
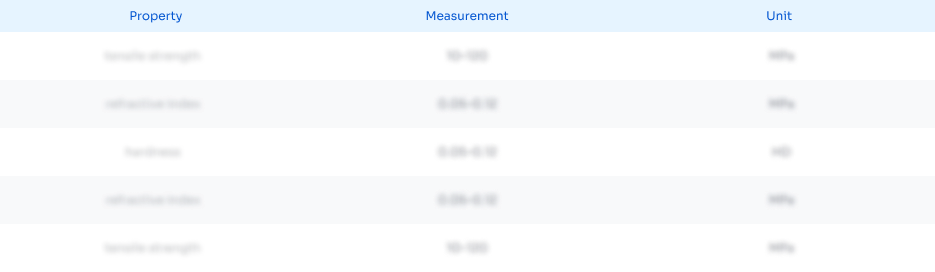
Abstract
Description
Claims
Application Information

- Generate Ideas
- Intellectual Property
- Life Sciences
- Materials
- Tech Scout
- Unparalleled Data Quality
- Higher Quality Content
- 60% Fewer Hallucinations
Browse by: Latest US Patents, China's latest patents, Technical Efficacy Thesaurus, Application Domain, Technology Topic, Popular Technical Reports.
© 2025 PatSnap. All rights reserved.Legal|Privacy policy|Modern Slavery Act Transparency Statement|Sitemap|About US| Contact US: help@patsnap.com