Optical fiber ring structure and optical fiber ring simulation temperature measurement structure
An optical fiber ring and optical fiber technology, applied in the field of optical fiber inertial navigation, can solve the problems of one-sided temperature distribution of the optical fiber ring, affecting the effect of temperature compensation, etc., and achieve the effect of optimizing the temperature compensation method and improving the accuracy
- Summary
- Abstract
- Description
- Claims
- Application Information
AI Technical Summary
Problems solved by technology
Method used
Image
Examples
Embodiment Construction
[0043] The following will clearly and completely describe the technical solutions in the embodiments of the present application with reference to the accompanying drawings of the present application. Apparently, the described embodiments are only some of the embodiments of the present application, not all of them. Based on the embodiments in this application, all other embodiments obtained by persons of ordinary skill in the art without making creative efforts belong to the scope of protection of this application.
[0044] The present invention provides an optical fiber ring structure, the optical fiber ring structure 4 is a hollow columnar structure and includes M layers of optical fibers arranged in the length direction of the optical fiber ring, M≥2, and the optical fiber ring structure 4 includes L optical fibers, L≥ 1. The i-th optical fiber is wound to form M arranged in the length direction of the optical fiber ring structure 4 i Layers of optical fibers, the number of ...
PUM
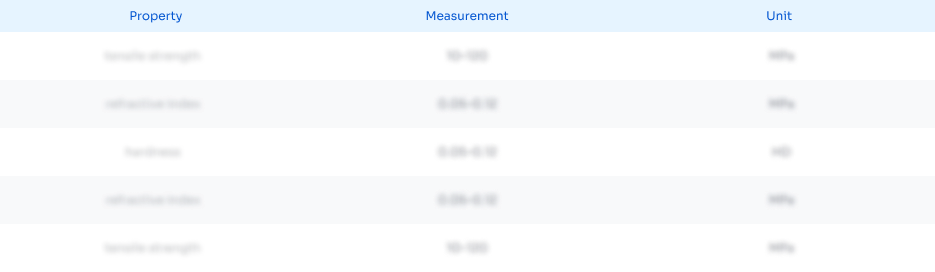
Abstract
Description
Claims
Application Information

- R&D
- Intellectual Property
- Life Sciences
- Materials
- Tech Scout
- Unparalleled Data Quality
- Higher Quality Content
- 60% Fewer Hallucinations
Browse by: Latest US Patents, China's latest patents, Technical Efficacy Thesaurus, Application Domain, Technology Topic, Popular Technical Reports.
© 2025 PatSnap. All rights reserved.Legal|Privacy policy|Modern Slavery Act Transparency Statement|Sitemap|About US| Contact US: help@patsnap.com