Roller kiln cooling system for foamed ceramic production
A foamed ceramics and cooling system technology, applied in the field of kiln thermal engineering, can solve the problems of increased product cracking, low thermal conductivity, and uneven pore size of foamed ceramics, so as to achieve good uniformity of pores, stable cooling process, Effect of reducing debugging loss
- Summary
- Abstract
- Description
- Claims
- Application Information
AI Technical Summary
Problems solved by technology
Method used
Image
Examples
Embodiment Construction
[0028] The solutions of the present invention will be described in detail below in conjunction with the drawings and specific implementation methods.
[0029] Refer to attached figure 1 And attached image 3 , with figure 1 It is a structural schematic diagram of the existing conventional roller kiln cooling system. The cooling system of the roller kiln refers to the collection of facilities from the kiln firing zone to the kiln tail to control the internal temperature drop of the kiln. After being fired in the firing zone, the ceramic body enters the cooling system to cool down. In the initial stage, the conventional wall and floor tile products can be quickly cooled to about 700°C. The volume change associated with the crystal transformation before 573°C is small, so rapid cooling can be carried out. Correspondingly, in the quenching zone immediately after the firing zone, a large amount of cold air is blown into the ceramics by an external blower in the quenching zone. T...
PUM
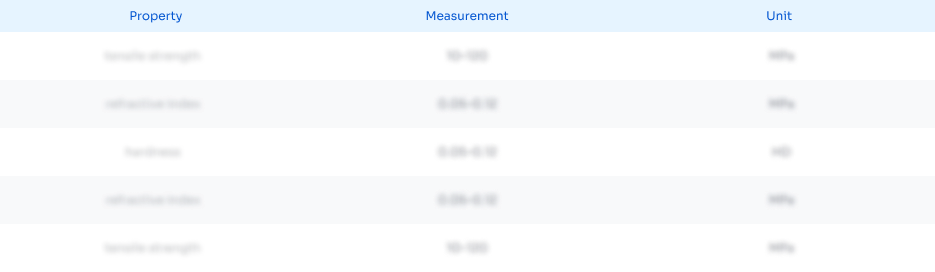
Abstract
Description
Claims
Application Information

- R&D
- Intellectual Property
- Life Sciences
- Materials
- Tech Scout
- Unparalleled Data Quality
- Higher Quality Content
- 60% Fewer Hallucinations
Browse by: Latest US Patents, China's latest patents, Technical Efficacy Thesaurus, Application Domain, Technology Topic, Popular Technical Reports.
© 2025 PatSnap. All rights reserved.Legal|Privacy policy|Modern Slavery Act Transparency Statement|Sitemap|About US| Contact US: help@patsnap.com