Truss type loading and unloading system and method suitable for multi-specification mining drill bits
A truss-type, multi-specification technology, applied in chucks, sustainable manufacturing/processing, manipulators, etc., can solve the problems of inability to realize automatic grabbing of mining drills, inability to meet usage requirements, and inability to meet the needs of automatic loading and unloading.
- Summary
- Abstract
- Description
- Claims
- Application Information
AI Technical Summary
Problems solved by technology
Method used
Image
Examples
Embodiment 1
[0050] Such as Figure 1 to Figure 6 As shown, the present embodiment provides a truss-type loading and unloading system suitable for multi-standard mine drill bits, including a truss-type manipulator 10, a flexible gripper 20 installed on the truss-type manipulator 10, a truss-type manipulator The feeding and positioning device 30 and the unloading tray 40 below the 10.
[0051] The flexible gripper 20 comprises: a vertical cylinder 21, a fixed seat 22 located at the bottom of the cylinder 21 and the cylinder piston rod 23 extends below the fixed seat 22, a lifting seat 24 connected to the bottom of the cylinder piston rod 23, and a fixed seat 22 located at the bottom of the cylinder piston rod 23. Two groups of arc-shaped support plates 25 that are hinged and symmetrical to each other with the fixed seat 22 at both ends, and two sets of connecting plates 26 that are symmetrically arranged on both sides of the lifting seat 24 and between the lifting seat 24 and the supporting...
Embodiment 2
[0067] This embodiment provides a truss-type loading and unloading method suitable for multi-standard mining drill bits, including:
[0068] Manually place the drill bit on the round tray of the feeding table. After the first laser sensor detects the incoming material of the round tray, the motor of the pre-positioning mechanism is started to drive the lead screw to drive the lead screw nut and V-shaped guide jaws to align the drill bit. Perform position correction and center pre-positioning; the truss-type mechanical arm driven by the servo motor drives the flexible gripper to transport the drill bit from the circular tray to the pneumatic three-jaw self-centering chuck of the rotary displacement mechanism; the pneumatic three-jaw self-centering chuck Clamp the drill bit and drive the drill bit to rotate slowly. During the rotation, the second laser sensor scans and recognizes the crown of the drill bit. When the crown positioning mark is recognized, the pneumatic three-jaw se...
PUM
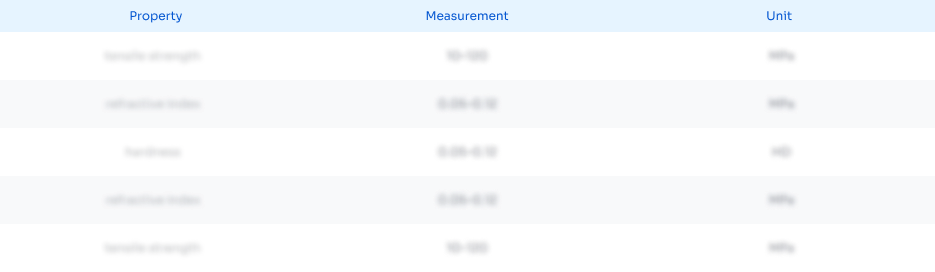
Abstract
Description
Claims
Application Information

- R&D
- Intellectual Property
- Life Sciences
- Materials
- Tech Scout
- Unparalleled Data Quality
- Higher Quality Content
- 60% Fewer Hallucinations
Browse by: Latest US Patents, China's latest patents, Technical Efficacy Thesaurus, Application Domain, Technology Topic, Popular Technical Reports.
© 2025 PatSnap. All rights reserved.Legal|Privacy policy|Modern Slavery Act Transparency Statement|Sitemap|About US| Contact US: help@patsnap.com